Smart Factories: 6 Benefits of Digitizing Your Manufacturing Floor
Success in manufacturing largely depends on efficiency, which takes the form of reducing operating expenses, maximizing materials, and reducing defects. Manufacturers who excel in these areas have a significant advantage over the competition, allowing them to build customer loyalty with high-quality products and offer lower prices.
Smart factories have emerged as an absolute game changer in this highly competitive field that focuses on efficiency. The technologies that power smart factories allow for a never-before-seen level of efficiency, product quality, and agility.
Turning a factory into a smart factory requires comprehensive digitizing by leveraging the latest advancements in core technologies, like AI, IoT, and data analytics. While it may not be an overnight initiative, you’ll realize the benefits of smart factories quickly after you upgrade.
What benefits can smart factories provide? We’ll be breaking down the core benefits that follow digitizing your factories, on top of further defining what separates a smart factory from a factory — keep reading to learn why you should start digitizing as soon as possible.
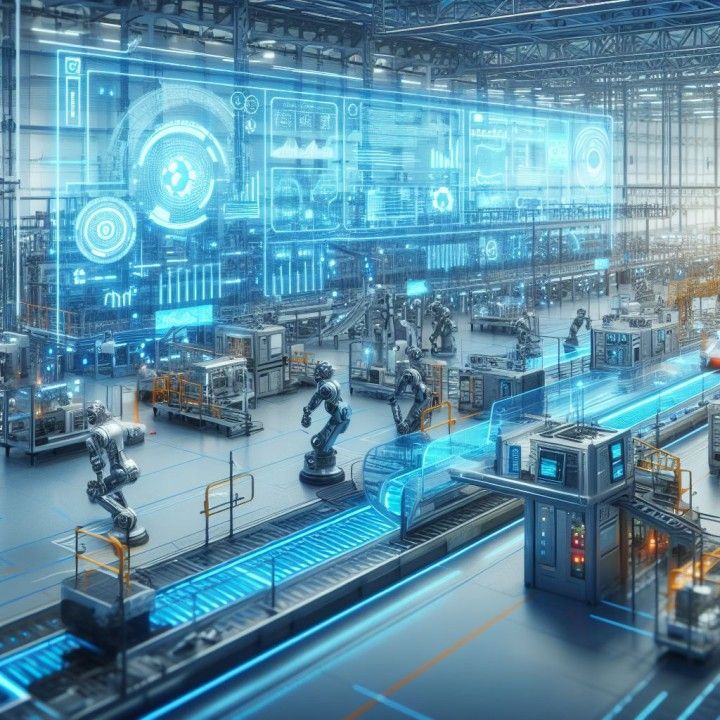
What is a Smart Factory?
A smart factory leverages a range of the latest technological advancements to become the pinnacle of modern manufacturing. These factories blend technologies to create an interconnected and hyper-efficient manufacturing environment.
At its core, smart factories leverage the following technologies:
- Internet of Things (IoT)
- Artificial Intelligence (AI) and Machine Learning (ML)
- Advanced automation
- Computer vision
These advanced technologies' exact applications will vary by industry and individual factory. Still, their presence and the ongoing focus on efficiency make a factory smart.
Leveraging these technologies enables seamless communication between equipment, systems, and humans — creating a significantly more agile and responsive manufacturing ecosystem.
Key Components of a Smart Factory
The abovementioned technologies have created specific components and capabilities used throughout a smart factor. A few of the core components of a smart factory are:
- Sensors: Embedded sensors in equipment used throughout operations allow for continuous capturing of relevant data, like temperature, vibration, or pressure, to name a few. Captured data can enable real-time monitoring and feed data into other components to power additional benefits.
- Connected devices: Equipment and machinery equipped with communication capabilities is a foundational aspect of smart factories. A previously siloed machine opens up and can share data with other machinery, enabling central control systems and real-time coordination.
- Data analytics: Advanced AI-driven analytics platforms can analyze the data generated by the above technologies. The result is actionable insights, predictive modelling, and advanced quality control.
- Cameras: High-resolution and thermal cameras aren’t new, but the technology behind them is. Advanced computer vision and ML models can leverage cameras for quality assurance and overall monitoring to create real-time improvements in manufacturing.
While the specific application varies, any smart factory will leverage all or most of these components to bring potent benefits to the entire operation.
Top 6 Business Benefits of Smart Factories
We can talk about technologies and components endlessly, but what does all that mean for manufacturing? Let’s step back from the marvel of modern technologies and look at the operational benefits they bring to the entire business.
1. Enhanced Operational Efficiency
Efficiency is the name of the manufacturing game, and smart factories are capable of maximizing throughput entirely unprecedentedly while reducing waste and defects. Let’s break down exactly how smart factories boost efficiency.
- Real-time monitoring: One of the most significant advantages of a smart factory is the ability to monitor all operations in real time. Embedded sensors and connected devices are constantly capturing data, creating a comprehensive view of the entire manufacturing process.
- Predictive maintenance: AI-driven predictive maintenance tools can leverage data captured by real-time monitoring systems to unlock entirely new capabilities. A predictive maintenance platform can create better schedules for inspections, planned downtime for maintenance, and forecasting when a machine will reach the end of its life.
- Resource optimization: Making the most of power and input materials is crucial for reducing operating expenses and increasing profits. Smart factories utilize data-driven insights to optimize everything from material usage to energy consumption. This can take the form of making adjustments by leveraging real-time data or historical data to produce valuable insights that inform managers' decisions.
2. Higher Product Quality
Maintaining high-quality products is critical in today’s competitive market and in essentially every industry. Smart factories are to produce higher quality end products by providing better quality control and ensuring consistency in production.
This high degree of quality control is made possible by automated inspection systems leveraging computer vision along with real-time feedback loops from embedded sensors. Cameras and sensors can instantly detect defects and any inconsistencies once they occur, which allows for fast corrective actions.
On top of a consistently higher quality product, the operation also reduces the likelihood of defective products making it to consumers, enhancing customer satisfaction and, in some scenarios, safety.
Additionally, these same capabilities allow for consistent manufacturing of the same quality products. Customers will come to expect a high-quality product, and you’ll be able to deliver it every time — improving your brand’s reputation with every order.
3. Increased Flexibility and Agility
The ability to quickly adapt to change demands, available resources, and disruptions is critical for modern manufacturers to stay competitive. There are several different ways smart factories keep you flexible, like real-time monitoring and AI-driven data analytics.
Real-time monitoring brings with it a wide range of benefits depending on how it's used and other supporting technologies. This new level of monitoring creates greater agility by helping managers quickly detect and address any possible issues and avoiding unplanned downtime.
When combined with advanced automation or AI, data from real-time monitoring systems can be evaluated by purpose-built models to better identify any deviations in product quality, productivity KPIs, or equipment functionality that enable rapid resolutions to these issues. This process creates an ongoing, flexible process to adjust to the current state of equipment and resources.
4. Enhanced Supply Chain Integration
Supply chain issues can slow down or entirely halt manufacturing operations. That’s why supply chain integration is such a powerful benefit — it allows you to stay on top of any upstream concerns.
An ideal integration provides visibility across your supply chain by leveraging data from your partners’ connected systems. You’ll be equipped to track the movement of raw materials, components, and finished products in real time. Any bottlenecks will be identified so you can find alternatives before operations are affected.
Additionally, this new level of connectivity creates enhanced collaboration for everyone involved. Sharing data between vendors and partners allows for better communication and coordination to build more resilient supply chains.
5. Cost Savings and ROI
Implementing smart factory technologies requires an upfront investment, including both time and funds. You’ll need to purchase sensors, connected devices, new IoT devices, and advanced software, depending on your specific needs.
However, the long-term financial benefits will almost certainly outweigh these initial investments. You’ll be able to cut costs dramatically by enhancing operational efficiency, reducing downtime, and optimizing resources.
For example, predictive maintenance helps cut costs and maximize returns by extending the life cycle of machinery and minimizing unplanned downtime. Inspecting and repairing equipment before it goes down helps make the most of your operating expenses.
Additionally, the increase in product quality and customer satisfaction leads to boosting revenue, expanding market share, and ultimately further increasing your return on investment (ROI). The overall cumulative benefits of smart factories will most likely result in a substantial ROI, making the initial investment well worth the costs.
6. Sustainability and Environmental Impact
Smart factories are inherently more sustainable due to their ability to maximize input resources and power. You can take these benefits even further by focusing specifically on becoming as sustainable as possible.
The right software, IoT devices, and embedded sensors can enable your smart factory to minimize its climate impact as much as possible. Efficiently using resources and reducing waste goes far in becoming a more sustainable, environmentally friendly manufacturing operation.
Digitize Your Manufacturing Floor — And Seek Out Digitized Partners
Manufacturers need to stay competitive in an increasingly digital world and global marketplace. Consistently offering high-quality products at a competitive price is necessary to remain profitable.
Investing in digitization may require upfront time and resource investments, but it will help you remain competitive and take your operation to the next level. Additionally, working with partners who have also embraced digital transformation in manufacturing will allow you to benefit from their data and integrations.
GN is leading the charge in the next wave of
digitizing manufacturing. We’ve already transformed our processes by leveraging the latest technologies, and we’re always staying aware of the next breakthrough that can take our processes even further.
Do you need a manufacturing partner who’s already upgraded to smart factories or any help making the change for your operation?
Contact us today — we’re ready to help enhance your entire operation.