CNC Machining Services for the Aerospace Industry
Leverage GN Corp’s CNC machining services to manufacture durable, high-quality aircraft parts.
GN Corp is a leader in precision aerospace CNC machining parts, and we have the experience, equipment, and reputation for taking on even the most challenging orders.
Why Does the Aerospace Industry Use CNC Machining?
High-quality aerospace machined parts are essential for organizations throughout the industry. However, aerospace is also a highly regulated industry, necessitating working with a CNC machining partner with the proper certifications and experience to keep you compliant.
GN’s aerospace CNC machining parts go through multiple quality assurance products that give you all of the benefits of this specialized machining process, such as:
- Producing complex, custom parts at scale
- Focuses on dependability and quality
- Ready to work with nearly any type of material your project requires
- Manufacture the parts you need on time and on budget
Aerospace precision parts CNC machining can take on complex tasks that demand accuracy. Working with GN Corporations ensures your aerospace parts are of the highest quality and ready to work.
Benefits of Using CNC Machining for Aerospace Parts
- Superior Performance: Failure in aerospace components can be devastating, which is why the industry is highly regulated and scrutinized. Parts must meet stringent performance, tolerance, and dimensional requirements. CNC machining makes these attributes possible without increasing costs.
- Lightweight: Aerospace parts must be light so the aircraft can take off and reduce fuel consumption while in flight. CNC aerospace machining can produce thin-walled components and work with necessary alloys to produce strong yet lightweight components ready for flight.
- High Efficiency: CNC machining leverages automation to achieve higher per-part speeds and shorten overall production cycles. GN’s Industry 4.0 processes leverage machine learning and automation throughout our workflows to save time without sacrificing quality.
- Reliable Precision: One primary reason why CNC machining aerospace parts has become so popular is because of the need for precision while tackling complex designs. CNC provides better accuracy and control to minimize defects and produce high-quality components.
- Affordability:
Per-part costs can be decreased when CNC machining is leveraged for rapid production. Manufacturers can reduce waste, labour hours, and rework due to the combination of automation and precision. Reducing defects creates significant savings for the entire batch.
Aerospace CNC Machining Applications in Aviation and Spaceflight
CNC machining
is widely used throughout aviation, aerospace, and spaceflight to manufacture components that demand precision and durability. Common use cases include valve components, electrical connectors, filter bodies, and oxygen generation components. Any faults in these areas can be devastating, leading companies to use CNC precision machining.
Materials for Aerospace Machined Parts
- Aluminum Alloy Series 2xxx: This series of alloys is combined with copper to create a high-strength and workable alloy. Precision aerospace CNC machining parts manufacturers use this alloy for machined parts such as fuselage structures and airplane wings.
- Aluminum Alloy Series 6xxx: By using magnesium and silicon, this alloy series is one of the most versatile aluminum alloys. The material provides better corrosion resistance, formability, and strength compared to some other options. Series 6xxx is widely utilized throughout many industries.
- Aluminum Alloy Series 7xxx:
Series 7xxx focuses on using zinc as the primary alloying element and can also include magnesium, copper, or chromium. The resulting alloy is strong and durable, making it widely used in defense and aerospace.
Our CNC Machining Capabilities
Unique CNC machining capabilities are why aerospace parts CNC machining manufacturing is one of the top methods in the industry. Multi-axis machines are at the core of this method.
Some of the most common CNC machines are:
The cornerstone of CNC machining is the 5-Axis milling machine. Our 5 axis CNC machine is capable of manufacturing polyhedrons and complex structural parts in a single operation.
Choosing the 9-Axis milling machine allows your CNC partner to manufacture more complex shapes, which is often necessary for the highly specialized components in the aerospace industry.
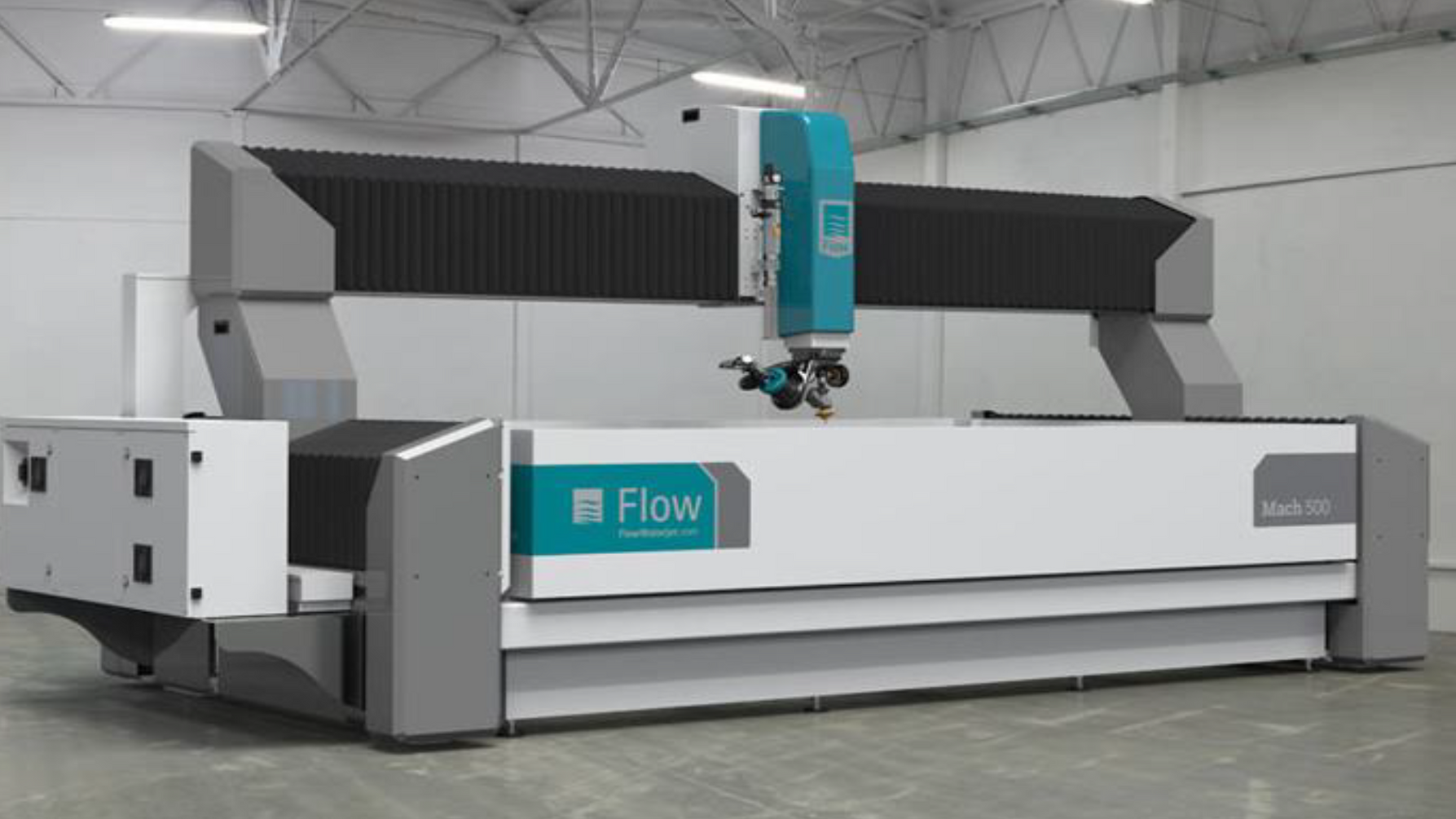
5-Axis Water Jet Cutters & Wire EDM
Similar to the standard 5-Axis milling machine, this version uses water jet cutters or wires to take on different materials without jeopardizing integrity with cuts.
Frequently Asked Questions
Make GN Corporation Your CNC Manufacturing Partner for Aerospace Parts
You need a certified, reputable, and dependable CNC manufacturing partner to take on your next order. Our CNC machining aerospace parts quotes consider all the elements of your order so we can provide you with both a cost and time estimate.
Ready to keep your project on budget and on time? Contact GN Corporations today to get a
quote for aerospace CNC machining.