Enhancing Quality in CNC Machining: 10 Paths of Digital Transformation
As new tools and technologies emerge, the manufacturing sector is no stranger to transformation. The first Industrial Revolution was powered by coal and assembly lines, but that’s not where manufacturing stopped — transformation has continued alongside new technologies, equipment, and requirements.
We’re in the fourth Industrial Revolution, a profound digital transformation powered by advanced technology. Although manufacturing has undergone significant technological transformation, a new wave of innovation has allowed for a new level of precision, efficiency, and cost-effectiveness.
CNC machining (Computer Numerical Control) is a prime example of how technology created this new method and continues evolving alongside new technologies.
So, let’s examine ten transformative technologies that improve
CNC machining services and explain why embracing digital transformation is critical for the industry's future.
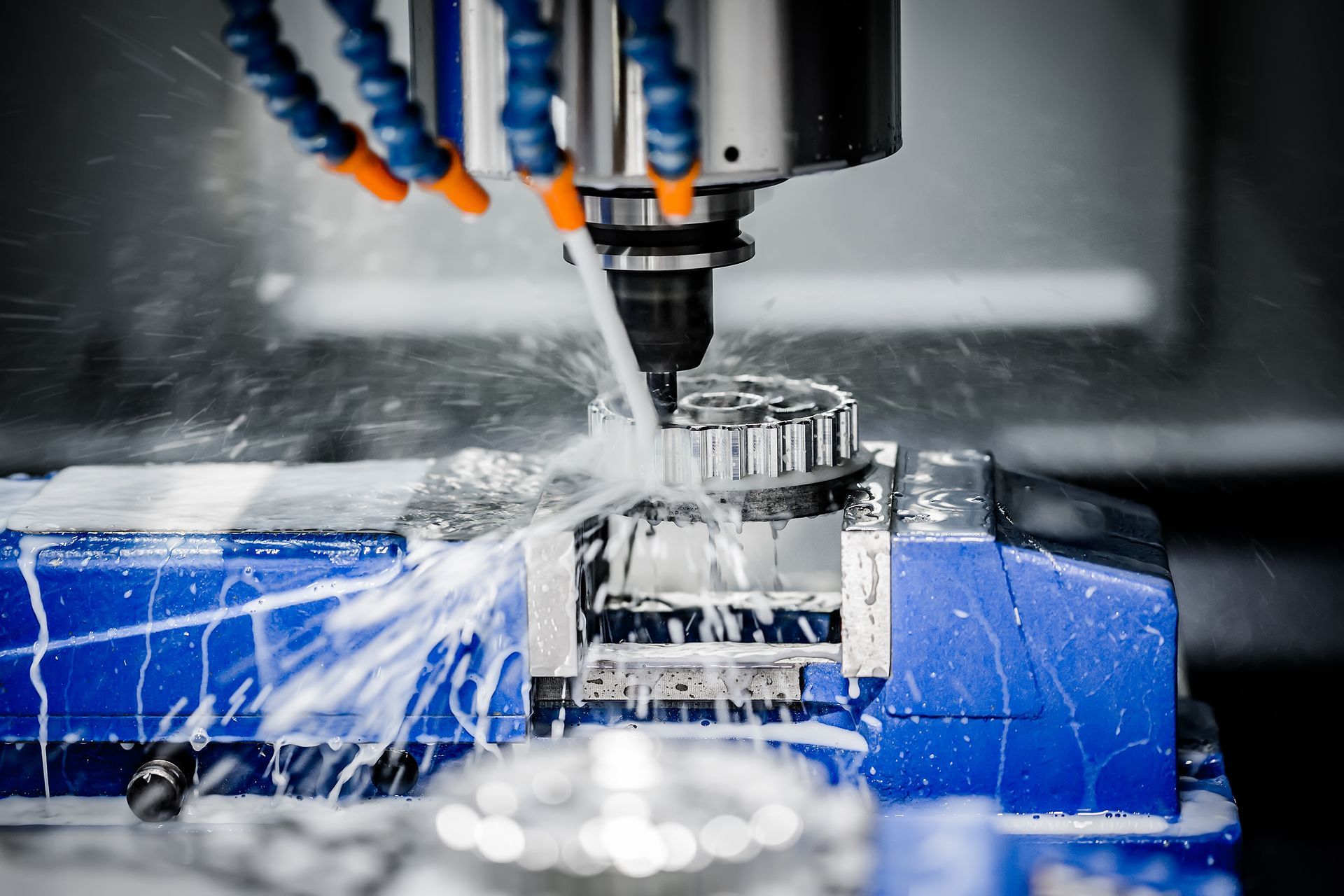
1. Smart Sensors and Real-Time Monitoring
Internet of Things (IoT) devices, especially smart sensors, are critical in enhancing precision and monitoring during production. These sensors collect real-time data on various parameters related to the CNC machining process. This data is analyzed to provide valuable insights during and after each production run.
For example, during a production run, smart sensors can detect anomalies or deviations from standard operating conditions, such as temperature or humidity, allowing corrective action to be taken.
The real-time monitoring capabilities of smart sensors allow for optimization, downtime reduction, and improved product quality in CNC machining. IoT devices extend equipment life and enhance operational efficiency and productivity by ensuring that machinery operates within optimal parameters.
2. AI-Driven Quality Assurance
AI-powered systems have been trained on historical data and equipped with computer vision, allowing for an entirely new level of AI-driven quality assurance. Machine learning models can analyze technical drawings of products to identify flaws that may otherwise go undetected.
Implementing AI-driven quality assurance allows CNC machining services to ensure consistent product quality, reduce waste, and enhance the quality of the end product.
3. Robotic Process Automation (RPA)
Robotic Process Automation (RPA) transforms manufacturing by automating repetitive tasks, improving consistency, and reducing errors.
Robots automate common tasks, including assembly line operations, material handling, and packaging. In assembly lines, robots can perform precise, repetitive tasks such as welding or screwing with high accuracy, ensuring uniform quality across products.
In material handling, automated guided vehicles (AGVs) transport materials within the factory, reducing the risk of human error and injury. Automating these processes allows manufacturers to increase productivity and free up specialized human workers to focus on higher-level responsibilities.
4. Advanced-Data Analytics
Advanced data analytics involves leveraging big data to refine manufacturing processes and improve product quality. Collecting and analyzing data from various sources can identify bottlenecks in production or optimize supply chain management, for example.
Advanced data analytics can also enable predictive maintenance. These AI algorithms can analyze vast data from production runs to identify subtle patterns and predict potential equipment failures before they occur—known as predictive maintenance. This proactive approach reduces unexpected downtime and maintenance costs.
Data is behind much of the latest digital transformation, collected by some technologies and leveraged by others.
5. 3D Printing Integration
Integrating 3D printing capabilities into manufacturing processes can lead to faster prototyping and error correction. This accelerates the development process and reduces the time to market for new products, especially in CNC machining.
Additionally, 3D printing can produce complex geometries that are difficult or impossible to achieve with traditional manufacturing methods, allowing for greater design flexibility. Regarding error correction, 3D printing can produce replacement parts on demand, minimizing downtime and maintaining production continuity.
By incorporating 3D printing, manufacturers can enhance innovation, reduce costs, and improve production efficiency.
6. Cloud Computing
Cloud computing facilitates real-time data access and collaboration across manufacturing facilities. By storing data in the cloud, manufacturers can ensure that all stakeholders can access the most up-to-date information, regardless of location.
This capability enhances collaboration and decision-making processes, as teams can work together more effectively with real-time data. Cloud-based solutions offer scalability, allowing manufacturers to adjust their IT resources according to their needs without significant capital investment.
Additionally, cloud computing supports advanced analytics and machine learning applications, enabling manufacturers to obtain deeper insights from their data and drive continuous improvement in their operations to support high-quality end products.
7. Virtual Reality (VR) for Training
Using Virtual Reality (VR) for training in manufacturing can significantly reduce human errors and enhance skill sets. VR provides a simulated environment where operators can practice tasks and procedures without facing real-world consequences.
This immersive training method allows employees to gain hands-on experience and develop muscle memory for complex operations. VR training can benefit high-risk tasks, enabling workers to learn and make mistakes in a safe, controlled setting.
VR helps ensure operators are better prepared and more competent, leading to higher efficiency, reduced errors, and improved safety in manufacturing environments.
8. Supply Chain Optimization
Digital tools are essential for streamlining supply chain operations to ensure timely material availability in manufacturing. IoT, AI, and advanced analytics provide real-time visibility into supply chain activities, enabling manufacturers to monitor inventory levels, track shipments, and predict potential disruptions.
These tools allow manufacturers to optimize inventory management, reduce lead times, and enhance overall supply chain efficiency. For example, predictive analytics can forecast demand patterns, allowing for better planning and resource allocation.
IoT devices can also provide real-time tracking of goods, ensuring that materials are available when needed, minimizing production delays, and enhancing overall operational efficiency.
9. Sustainability Through Digitalization
Digital transformation helps manufacturers reduce waste and optimize energy use, contributing to sustainability efforts. By implementing advanced technologies such as IoT, AI, and data analytics, manufacturers can monitor and manage resource consumption more effectively. For instance, IoT sensors can track energy usage in real-time, identifying areas where efficiency can be improved. AI algorithms can optimize production processes to minimize waste and reduce emissions.
Additionally, digital tools enable more precise control over supply chains, reducing excess inventory and minimizing material waste. Through digitalization, manufacturers can achieve significant environmental benefits, aligning their operations with sustainability goals and reducing their environmental footprint.
10. The Current and Future Potential of Advanced Digital Tools
Digital transformation offers numerous benefits for the manufacturing sector, including increased efficiency, improved product quality, and enhanced sustainability. Technologies like IoT, AI, cloud computing, and advanced analytics allow for precision manufacturing, creating an entirely new level of quality and efficiency.
As manufacturers embrace these evolved digital tools, productivity, efficiency, and durability in CNC machining services will continue to improve. That’s why it's important to partner with a supplier leading the charge towards next-gen manufacturing.
GN has developed GN 4.0, a technology-driven approach to Industry 4.0 that offers companies high-quality services. Are you ready to partner with a cutting-edge CNC precision machining service provider?
Request a quote today to get started.
FAQs
What is digital transformation in CNC machining?
Digital transformation in CNC machining involves integrating advanced technologies like IoT, AI, and cloud computing into CNC processes. This integration enhances precision, automates key processes, and enhances data analysis, producing more efficient and accurate production.
Overall, digital transformation helps cut costs and improve process accuracy, ultimately allowing CNC manufacturers to ensure consistent quality of end products.
How does digital transformation affect production efficiency?
Digital transformation boosts production efficiency by enabling real-time monitoring, predictive maintenance, and automation. These technologies minimize downtime, streamline workflows, and optimize resource use.
Additionally, enhanced data analytics improve decision-making, leading to faster, more accurate production processes, reduced waste, and increased overall productivity.
Can digital transformation in CNC machining lead to better compliance with industry regulations?
Digital transformation in CNC machining can lead to better compliance with industry regulations. The advanced monitoring and data analytics capabilities allow for precise control and documentation of all relevant processes.
Automated systems can also track core compliance metrics, allowing organizations to identify deviations in real time, implement corrective actions, and ensure ongoing compliance with all regulatory standards.
What are the specific benefits of digital transformation for the aerospace and automotive industries?
Digital transformation offers numerous benefits for the aerospace and automotive industries, including improved precision, enhanced quality control, and reduced production costs. Advanced analytics optimize design and manufacturing processes, while IoT and AI enable real-time monitoring and predictive analytics.
The result for the aerospace and automotive industries is increased efficiency, safety, and faster time-to-market for new products.