The Role of CNC Machining in Modern Defense Manufacturing
The defense industry always pushes the envelope of technological innovations, manufacturing processes, and materials engineering. Any organization involved in defense manufacturing strives to establish and maintain a strategic advantage.
Advanced Computer Numerical Control (CNC) machining is a pivotal technology driving defense innovation. Advanced CNC machining has transformed how defense components are designed, prototyped, and manufactured by offering unprecedented precision and durability.
CNC machining requires accuracy and defect-free components in several industries, as flaws can have devastating results. Defense, aerospace, and automotive can all benefit from components produced with CNC machining.
So, we’ll be honing in on the defense industry and exploring the role of advanced CNC machining in modern defense manufacturing. Read on to learn more about this transformative manufacturing method and why it’s become critical in defense.
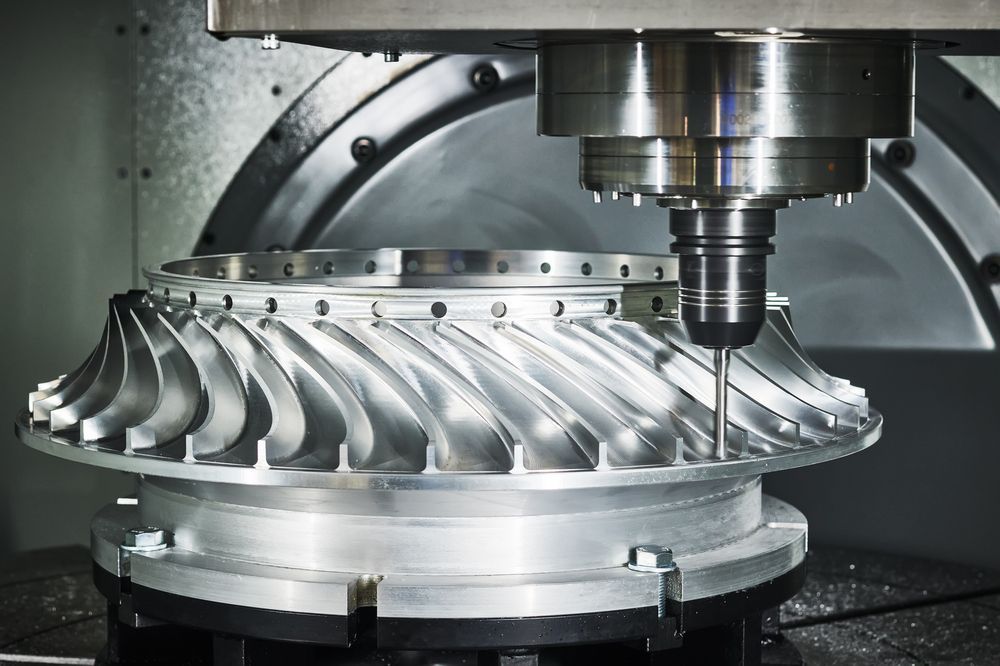
Understanding Advanced CNC Machining
CNC machining has grown by leaps and bounds in recent years as technological advances have reached new levels. While CNC machining isn’t a brand new practice, it’s benefitted from leading-edge technologies that improve the accuracy and dependability of end products.
What is CNC Machining?
CNC machining involves pre-programmed computer software that controls the movement of factory tools and machinery. This advanced process can control a wide range of complex machinery, from lathes to mills to grinders.
Using
CNC machining, three-dimensional cutting tasks can be accomplished with a single automated routine, creating profoundly improved precision and efficiency compared to other processes.
Additionally, because of how CNC machining works, it provides consistent results with accuracy and speed. The defense industry can depend on every individual component performing as designed.
Evolution of CNC Machining
While the latest version of CNC machining leverages advanced technologies, the overall field isn’t new. CNC machining began in the 1940s and 50s when the first numerical control (NC) machines were developed. Then, as computing steadily grew, the 1960s began seeing the transformation from NC to CNC.
Over the decades, advancements in computing and machinery have contributed to steady improvement in CNC machining. Modern CNC machines are highly sophisticated and capable of unprecedented precision and highly durable end products. Various industries have pivoted to advanced CNC machining to benefit from precise, reliable end products.
Applications of Advanced CNC Machining in Defense Manufacturing
Where exactly does CNC machining come into play in the defense industry? Not every component requires what CNC machining offers, such as non-essential components that may be perfectly fine with other manufacturing methods.
So, let’s explore where CNC machining comes into play and how it helps the defense industry stay innovative and productive.
Precision Parts Production
Components in the defense industry must be precise and reliable, as deviations or defects can have devastating consequences. CNC machining excels in manufacturing intricate parts that perform as designed.
A high level of precision is crucial throughout the defense industry, where even the slightest deviations can compromise safety and performance. CNC machines can produce precise components for aircraft, missiles, and defense systems with consistent precision that translates to real-world results.
Customization and Prototyping
The defense industry always pushes the envelope and innovates new equipment and technologies to stay ahead of adversaries. Core aspects of this ongoing innovation are prototyping and customization.
The speed of prototyping directly affects how quickly a new piece of equipment can be manufactured at scale and deployed. CNC machining can take designs and create a prototype rapidly, allowing engineers to evaluate their design and determine if it needs more work or is ready for the next step.
Additionally, customization in the defense industry allows for components to be used in different specific use cases by making smaller changes. Having different versions of designs loaded on a CNC machine is highly efficient and allows production runs or prototyping to produce these variations rapidly.
Large-Scale Production
Advanced CNC machining for the defense industry requires large-scale production once the prototyping phase is complete. CNC machining supports large-scale production through advanced automation, creating consistent results across all components.
This level of scalability is vital for producing large quantities of components required in various defense equipment, such as military vehicles and weapons systems. CNC machining can take on these high-quantity production runs while ensuring every part is identical and meets strict quality standards, reducing the risk of component failure.
Benefits of Advanced CNC Machining for the Defense Industry
CNC machining has plenty to offer nearly every industry, but what benefits does it offer defense? We’ve already explored some of these benefits, so let’s drill down into why the defense industry and CNC machining are a perfect pair.
Enhanced Precision and Accuracy
Components in defense are one part of a larger piece of equipment that must work when needed most. Small deviations from specifications can create accidents, reduce effectiveness, or create unplanned downtime in demanding situations.
That's why precision and accuracy are the most significant benefits of opting for CNC machining. CNC machining offers tight tolerances with a never-before-seen level of accuracy. The multi-axis control arms allow for following intricate components and maintaining precision across every component.
Increased Production Speed
Production speed is crucial in prototyping and large-scale runs, which are necessary to keep the defense industry moving forward. CNC machining can manufacture complex parts and meet a high degree of precision repeatedly — all it takes is programming the design into the machine once.
From there, the production run is entirely automated, with little human intervention necessary, depending on the task.
As a result, you’ll benefit from faster production timelines, be ready to meet deadlines and respond to any urgent operational needs.
Cost-Effectiveness
Working with a machining partner sidesteps the need for initial investments in machinery and skilled workers, fast-forwarding to cost-effective operations. CNC machining reduces labor costs, material consumption, and errors in production — each cutting costs in the total production run.
Managing costs is critical in the defense industry. Working with a CNC machining partner is a cost-effective way to produce high-quality, reliable components.
Technological Advancements and Innovations in CNC Machining
CNC machining leverages several advanced technologies to provide a high level of precision and durability.
Advancements in both hardware and software continually help CNC machining improve. Let's explore how the latest wave of technology is put to work in CNC machining.
Integration with Advanced Software
Software is at the heart of CNC machining, as programmed instructions dictate the entire process.
Advanced machine learning software has taken this utility to the next level by better informing each task, identifying any deviations, and immediately correcting them or triggering alerts.
Computer vision and other sensors are able to significantly improve the manufacturing process by leveraging real-time data about each task, unlocking real-time monitoring.
Multi-Axis Machining
CNC machining relies on manipulating the material along several planes to make each cut. In the past, 3-axis controls were the standard and did provide some benefits over other methods.
Now,
5-axis and
9-axis machines have unlocked an entirely new level of control and capabilities. This advanced equipment is able to seamlessly rotate and maneuver material across a significant range of motion.
The result is that extremely intricate designs can be manufactured without the need to stop the machine from changing materials. Each task can be carried out precisely and with tight tolerance.
Partner with a Leading CNC Machining Provider Today
The defense industry requires tight tolerance and components ready to perform under intense conditions. Even a small component that breaks under pressure or has an overlooked defect can create issues in high-stakes situations.
CNC machining offers a never-before-seen opportunity for more accurate manufacturing that doesn’t jeopardize the durability of materials, creating dependable components.
However, buying your own CNC machines and hiring skilled experts to operate them involves a significant investment. While CNC can be cheaper over time, you might not have the budget or expertise to make it a worthwhile investment.
It’s well worth working with a partner instead of handling it in-house. GN has decades of experience in defense manufacturing, and we know how to handle everything from prototyping to large-scale manufacturing.