Real-Time Process Optimization: How Machine Learning Fine-Tunes CNC Parameters
Efficiency and precision are critical in manufacturing, making optimizing processes highly valuable to the entire operation. However, traditional manufacturing optimization methods relied on manual adjustments, tuning, and post-production analysis.
Fortunately, with the rise of machine learning (ML) and real-time data analytics, manufacturers can now fine-tune CNC parameters dynamically to ensure maximum efficiency, precision, and cost savings.
Real-time process optimization allows CNC machines to self-adjust based on sensor data and predictive modelling. Let’s explore how the latest technologies unlock this capability and how it can transform your business.
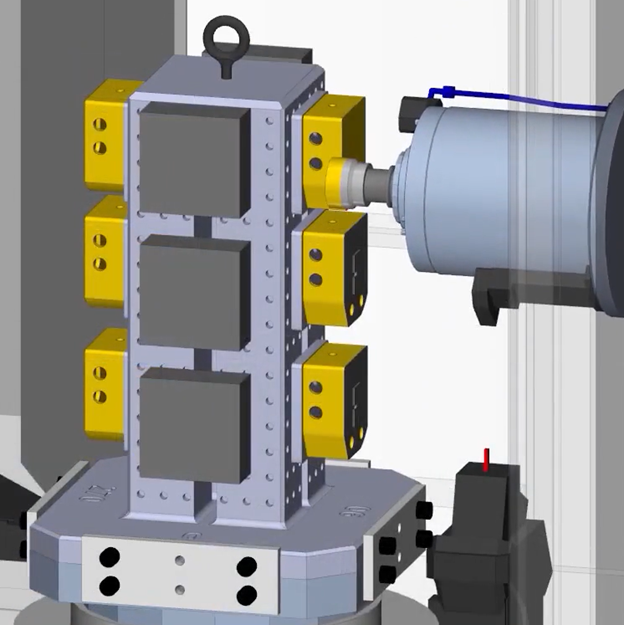
Defining Real-Time Process Optimization
Real-time optimization refers to the continuous and immediate adjustment of machining parameters based on real-time sensor data and predictive analytics.
Traditional optimization involves static, predefined settings that can slow operations if issues arise. Instead, real-time optimization adapts dynamically, responding to changing conditions such as tool wear, material inconsistencies, and environmental variations.
Why does all this matter? Speed and agility can make a significant difference in a competitive manufacturing landscape. Implementing real-time process optimization offers far-reaching benefits, including:
- Fewer defective parts as immediate adjustments prevent defects before they occur.
- Optimal cycle times, which reduces machining time without compromising quality.
- Preventing unplanned downtime due to early detection of anomalies allows for proactive maintenance.
Once you’ve implemented all the right components, real-time process optimization will reduce defects and maximize operating expenses.
Key Components
Real-time tuning of CNC parameters relies on the integration of hardware and software components, such as:
- CNC machines are the core of the manufacturing process.
- Sensors collect real-time data on machine conditions.
- Analytics platforms process and analyze sensor data.
- AI tools utilize machine learning algorithms to make real-time adjustments.
Machine Learning Basics for CNC Machining
CNC machining isn’t a brand-new technology, but it’s been steadily evolving right alongside tech advancements ever since the first CNC machine in the 1940s. Machine learning is the latest to be applied to CNC machining to bring several valuable benefits to the entire organization.
Types of ML Approaches
Machine learning is crucial to effective real-time optimization. There are three common approaches to training ML algorithms that can be applied to CNC machining, which are:
- Supervised learning: This type of learning trains models using labeled datasets, allowing them to predict outcomes based on historical data.
- Unsupervised learning: This learning method allows models to identify patterns in unlabeled data, which can be useful for detecting anomalies.
- Reinforcement learning: This learning method involves continuous learning based on feedback from the machining process, allowing for adaptive optimization.
How ML Models Learn from Data
CNC machining generates vast amounts of real-time data, such as data from the following components:
- Spindle speed
- Tool wear levels
- Feed rate
- Torque and cutting forces
Machine Learning: The Backbone of the GN 4.0 Platform
Our GN 4.0 platform uses machine learning to refine machining processes. This system integrates real-time data from IoT-enabled CNC machines, enhancing decision-making and process efficiency.
Data Collection and Analysis in Real Time
Process optimization depends on far-reaching data collection and rapid data analysis. Let’s break down a few moving pieces that all need to be in place to fully maximize the benefits of real-time optimization.
Sensors and IoT-Enabled CNC Machines
Several types of sensors can feed data to the control system. A few common types of sensors are:
- Vibration sensors that detect anomalies in machine stability.
- Thermal sensors that monitor temperature fluctuations to prevent overheating.
- Current sensors that track power consumption for efficiency monitoring.
These sensors feed continuous data to the control system and form the backbone of real-time analytics.
Data Pipeline Architecture
The nuts and bolts of real-time optimization depend on consistently capturing data and implementing valuable changes. A high-level overview of the pipeline that turns data into an optimized process includes the following:
- Sensor data reflects raw data from CNC machines.
- Edge processing performs initial data filtering and analysis near the source.
- Cloud or local servers transfer data for deeper analysis.
- ML model predictions analyze patterns.
- The CNC machine self-adjusts parameters in real-time.
Latency and Bandwidth Considerations
You need real-time responsiveness, so optimizing data transmission latency and bandwidth efficiency is crucial. Technologies such as edge computing and 5G connectivity can enhance real-time decision-making.
How Machine Learning Fine-Tunes CNC Parameters
We’ve explored some aspects of how machine learning is used to fine-tune CNC processes. Now, let’s explore how this combination works in practice.
Dynamic Adjustment of Speeds and Feeds
Machine learning algorithms continuously evaluate real-time data to dynamically adjust the following parameters:
- RPM (rotations per minute)
- Feed rates
- Depth of cut
CNC machines achieve optimal efficiency and minimize tool wear by fine-tuning these parameters.
Tool Wear Compensation and Coolant Flow
Tool wear and tear can create premature costly repairs or replacements. ML models can predict tool wear by monitoring the following data points:
- Changes in cutting forces
- Surface finish quality
- Acoustic emissions
This predictive capability allows proactive tool replacement, reducing costs and ensuring high part quality.
Additionally, real-time temperature data enables adaptive coolant flow adjustments. This utility can go far in preventing overheating and maintaining consistency in key processes.
Predictive Alerts and Alarms
AI-driven systems can trigger alerts for human intervention before failures occur by detecting anomalies or gradual performance degradation. These alarms and alerts can go far in preventing downtime or degraded quality.
Benefits and ROI of Real-Time Optimization
What are the key benefits of implementing real-time process optimization? There are several far-reaching benefits for the entire operation, including:
- Increased throughput and efficiency: Dynamic adjustments reduce machining cycle times, eliminating bottlenecks and boosting overall productivity.
- Higher quality and consistency: Continuous real-time corrections maintain tight tolerances, improving product quality and fewer rejected parts.
- Cost savings: Factors like reduced scrap, lower tool replacement costs, and energy efficiency gains add to cost savings throughout the process.
- Scalability: A well-structured ML platform can scale across multiple CNC machines and manufacturing sites, providing consistent optimization benefits enterprise-wide.
Key Challenges and Considerations
There are several challenges that you’ll need to be aware of in order to successfully implement real-time process optimization, such as:
- Data quality and volume: Accurate sensor readings and comprehensive data coverage are essential. Poor data quality can lead to incorrect model predictions and suboptimal machining decisions.
- Model complexity and interpretability: Highly complex ML models can function as “black boxes,” making it difficult to interpret their decision-making process. Implementing explainable AI techniques can enhance transparency and trust.
- Integration with legacy equipment: Older CNC machines may require retrofitting with modern sensors and control units to fully leverage real-time optimization capabilities.
- Skilled workforce: Machine learning-driven CNC optimization requires skilled personnel who understand machining operations and AI principles. Training programs can bridge this knowledge gap.
Looking Ahead: Future Trends in ML and CNC
What might the future hold? A few technologies steadily changing the industry are:
- AI-driven autonomy: Future advancements in AI will enable CNC machines to make increasingly complex decisions with minimal human oversight.
- 5G Connectivity and edge computing: Adopting faster networks and localized data processing will enhance real-time decision-making capabilities.
- Digital twins: Virtual simulations of CNC machines will allow manufacturers to optimize processes in a digital environment before implementing them in real production.
- Expanding applications: AI-driven CNC optimization will significantly benefit industries such as aerospace, automotive, defense, and high-tech manufacturing.
Partner with GN Corp to Benefit from Our Real-Time Optimization
Real-time process optimization, driven by machine learning, represents a major leap forward in CNC machining efficiency. Manufacturers need to implement the right systems, while clients must prioritize partners leveraging the latest technologies.
GN Corp is an industry leader in leading-edge manufacturing processes. Is it time to step into the future and benefit your next production run?
Book a demo today and learn more about our processes.