How Advanced CNC Machining Enables Automotive Component Manufacturing
The automotive industry has come a long way, thanks to CNC machining. From high-performance engines to advanced safety components, modern vehicles rely on precision-machined parts that weren’t possible just a few decades ago.
CNC technology continues evolving, making production faster, more accurate, and more efficient. Manufacturers can now create complex components with tight tolerances, improving performance and reliability.
Keep reading to learn how GN uses this cutting-edge technology to manufacture engine blocks and powertrains, transmissions and drivetrains, brakes, safety-critical parts, and more while exceeding quality assurance and inspection standards.
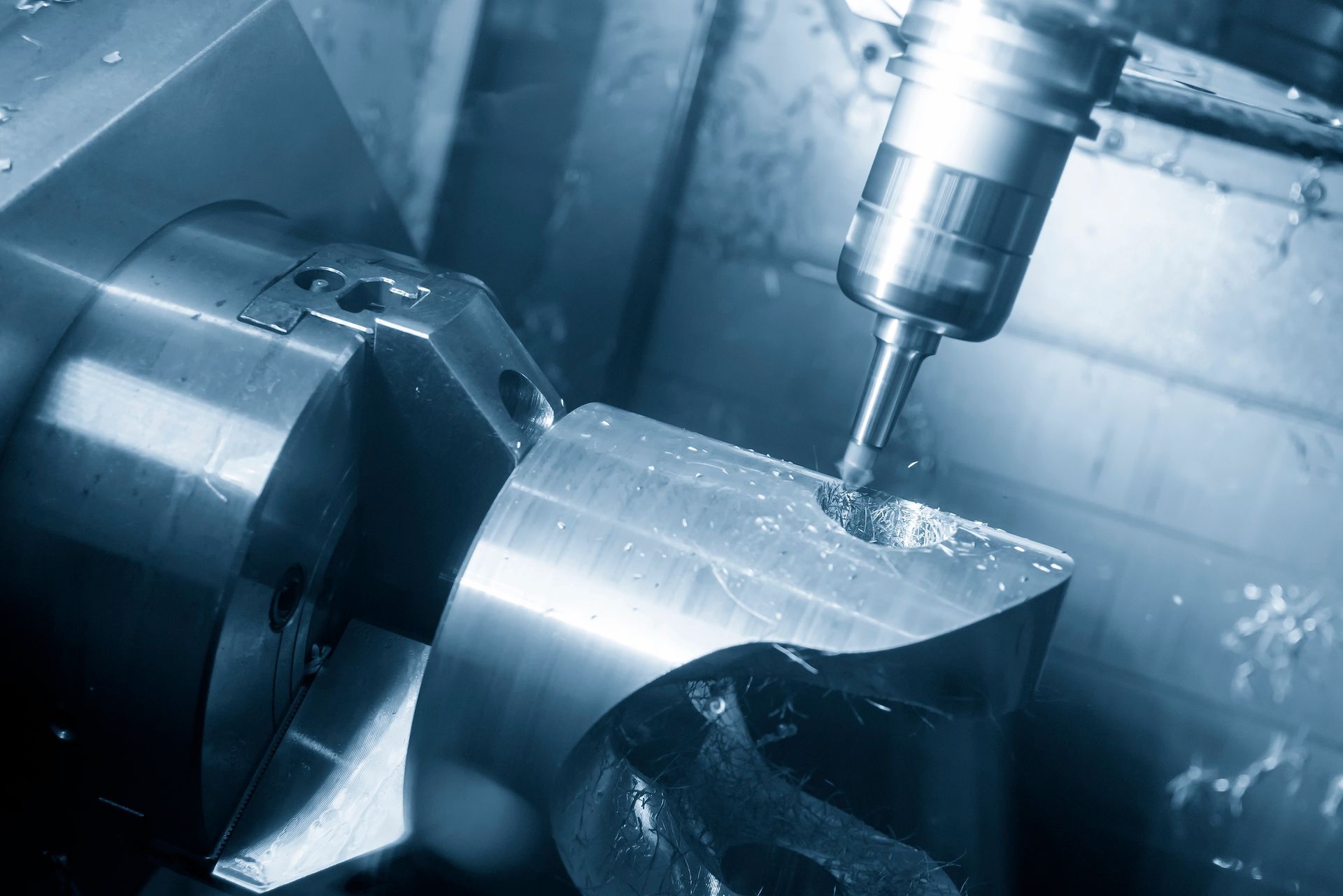
Engine and Powertrain Components
Modern engines demand extreme precision, and automotive CNC machining makes that possible. CNC technology ensures every component, from pistons to camshafts, meets exact power, efficiency, and durability specifications.
Engine Blocks
Every vehicle motor starts with an engine block. CNC milling carves out pathways for coolant, oil, and combustion, ensuring smooth performance down to the micron. Precision is everything since even the tiniest flaw can mess with heat dissipation, lubrication, or longevity.
With CNC milling, every cut is automated for extreme accuracy, creating intricate internal structures while holding tight tolerances. The result? More efficient combustion, longer engine life, and peak performance.
CNC machining is an environmentally friendly method as it generates less waste than traditional manufacturing techniques. The precision of CNC systems means less material is wasted, and the ability to recycle scrap material helps reduce environmental impact.
It also accelerates production timelines, allowing
manufacturers to produce high-quality engine blocks in large volumes without sacrificing consistency. Each machined engine block meets the same rigorous standards, ensuring every engine performs as expected.
Cylinder Heads and Pistons
Cylinder heads and pistons are the core of an engine’s combustion process, controlling how fuel and air mix, ignite, and power each stroke. The valves' positioning and the combustion chamber's shape work together to maximize performance, efficiency, and power.
The slightest changes in valve placement or chamber shape can throw off power, fuel efficiency, and emissions. CNC machining keeps every cylinder head precise, ensuring a smooth and consistent combustion process.
CNC machining cuts pistons with extreme precision for a tight fit while still allowing movement. Automated CNC processes ensure every piston matches its specs, preventing variations with excessive friction, uneven wear, or engine inefficiencies. These processes are especially critical in high-volume production, where maintaining uniformity across thousands of units is crucial.
CNC systems also adapt to the specific coatings required for pistons, ensuring optimal thermal and wear resistance in high-performance engines. Every material demands a different machining approach, from lightweight aluminum to rugged cast iron. CNC systems automatically fine-tune cutting speeds, tooling, and coolant flow to handle these differences while maintaining precision.
Crankshafts and Camshafts
Crankshafts and camshafts are constantly in motion, transferring power and timing the movement of engine components. CNC machining shapes these rotating parts precisely, maintaining balance and reducing mechanical stress.
A minor imbalance in a crankshaft can cause vibrations that lead to excessive wear and tear on bearings, seals, and other engine components. CNC turning and milling ensure these parts meet exact dimensions, preventing performance issues.
Crankshafts and camshafts need a flawless finish to reduce friction, prevent heat buildup, and extend lifespan. CNC machining delivers that polished surface with built-in inspections during machining, catching and correcting even the smallest deviations in real-time.
Advanced finishing techniques, such as precision grinding, are applied to these components to ensure each part has the smoothest surface possible, reducing friction and wear for optimal engine performance.
Transmission and Drivetrain Components
A vehicle's transmission and drivetrain work together to turn engine power into movement, so they must be built accurately.
Transmission Housings
The transmission housing protects and aligns the internal parts, ensuring the vehicle runs optimally. Automotive CNC machining places every hole, channel, and mounting surface meticulously, preventing misalignment that can cause shifting, leaks, or mechanical failures.
These housings usually begin as complex castings requiring several machining steps to improve their structure. Mills and lathes remove extra material, create channels for lubrication, and add finishing touches to reduce maintenance.
Advanced simulation techniques can predict potential wear and stress points in transmission housings, allowing for proactive design adjustments that improve longevity.
Gear Sets and Differentials
Gears must fit perfectly for smooth power transfer. Even the slightest mistake in tooth shape or alignment can lead to grinding, wear, and performance issues. CNC machining creates flawless helical and bevel gears, shaping each tooth to exact specs.
Specialized tools, multi-axis machining, and precise programming ensure that gears engage effortlessly, reducing noise and boosting efficiency. The same precision is used for differentials, where CNC technology helps balance power distribution between wheels with tight tolerances.
CNC technology makes it possible to create the intricate gear profiles necessary for advanced transmission systems in electric and hybrid vehicles that demand top-notch precision and performance.
Chassis and Suspension
A car’s chassis and suspension keep rides smooth, handling sharp, and stability locked in. These parts require serious strength and precision machining to perform safely and reliably on the road.
Control Arms and Knuckles
Control arms and steering knuckles connect the wheels to the chassis, ensuring uninterrupted movement and steady suspension. These parts endure everything from potholes to sharp turns, so they need to be tough and precise. CNC machining perfectly fits pivot points and mounting surfaces, ensuring your suspension delivers flawless handling and even tire wear.
Vehicles have different material needs, for example, steel for durability, aluminum for weight reduction, or composites for high-performance builds. CNC machining adapts to each, fine-tuning cutting speeds and tooling to ensure consistency.
Steering Components
A vehicle’s steering system relies on racks, pinions, and knuckles to maintain stability and responsiveness. CNC machining aligns each part meticulously, reducing play in the steering mechanism and improving control.
CNC technology also supports
quality control measures like stress and hardness tests, ensuring that every component meets safety standards before installation.
Shock Absorber Mounts and Suspension Links
Shock absorbers and suspension links help vehicles adapt to varying road conditions, reducing vibrations and improving ride comfort. Manufacturers must produce these components identically to ensure reliable performance over thousands of miles.
Automotive CNC machining ensures consistent dimensions for accurate installation and streamlined movement with minimal friction and wear. The right surface finishes also help prevent corrosion, extending the lifespan of critical suspension parts.
Brake and Safety-Critical Parts
Brakes directly impact safety and performance. CNC machining creates these parts accurately, ensuring they function without failure under high stress and heat conditions.
Precision machining guarantees dependable operation when it matters most, from brake callipers to anti-lock braking system (ABS) components.
Brake Callipers and Rotors
Brake callipers and rotors must withstand intense heat and pressure while maintaining consistent braking force. Slight variations in machining can cause uneven wear, reduced stopping power, or unwanted vibrations.
CNC milling and drilling create precise rotor slots and ventilation holes, optimizing heat dissipation and ensuring smooth braking. By maintaining tight tolerances, CNC machining helps prevent warping, extends component service life, and improves vehicle safety.
ABS Components
The ABS uses sensors, valves, and control units to stop the wheels from locking up during sudden braking. To work correctly, these parts must be precisely machined so everything fits and functions properly. Reliable machining ensures these crucial parts perform as expected on the road.
Body and Interior Metal Components
Automotive CNC machining creates metal components that boost a vehicle’s strength and durability while keeping weight in check. From dashboard frames to door hinges, every part needs to be tough, lightweight, and fit as intended.
Structural Brackets and Mounts
Brackets and mounts support seats, seatbelts, and dashboards. These parts require precise hole alignment to ensure a secure fit and streamline assembly.
CNC machining allows manufacturers to create complex brackets from lightweight, durable metals, balancing strength with minimal added weight. This is especially important in modern vehicles, where reducing mass helps improve fuel efficiency without compromising safety.
Dashboard Frames and Door Hinges
Dashboard frames hold critical controls and instruments, so every cut must be exact. Any miscalculation can lead to misaligned panels, rattles, or a weaker structure.
CNC machining ensures a perfect fit with tight tolerances. Door hinges also need precision to function correctly and last for years. Automated CNC systems produce these parts in large numbers while keeping quality high, ensuring every hinge works flawlessly.
Advanced Materials and Emerging Technologies
Automotive manufacturers are constantly pushing the limits of materials to make vehicles faster, more fuel-efficient, and safer. CNC machining makes it all possible by crafting intricate parts from strong, lightweight, and durable materials that keep everything running at its best.
As the industry shifts toward EVs and more sustainable manufacturing methods, automotive CNC machining continues adapting, making it easier to work with new materials and integrate emerging production techniques.
Hybrid machining, additive manufacturing, and advanced finishing technologies transform automotive components and production. These innovations improve performance, extend lifespan, and allow more complex designs.
Aluminum Alloys and Composites
Lightweight materials like aluminum alloys and composites are revolutionizing modern vehicles. Less weight means better fuel efficiency and sharper handling, acceleration, and braking.
CNC machining shapes these materials into strong, precise components without adding bulk. Aluminum's excellent strength-to-weight ratio is ideal for engine parts, suspension systems, and structural components.
Advanced CNC techniques, like high-speed milling and multi-axis machining, create intricate designs, including hollow sections that reduce weight while staying durable. These methods also ensure uniform thickness and smooth finishes, helping high-performance vehicles manage heat effectively.
Composites like carbon fibre-reinforced polymers can be challenging to machine since their layers can separate under too much pressure. CNC routers and waterjet cutting systems accurately shape these materials, preventing fraying and maintaining their strength.
Titanium and High-Performance Materials
High-performance vehicles, like luxury sports and race cars, rely on titanium and other specialized alloys for key components. Machining titanium requires specialized cutting tools and cooling methods since its hardness can quickly wear down tools and generate too much heat.
Multi-axis CNC milling and turning give manufacturers the precision to build complex titanium parts. Titanium's lightweight properties and impressive tensile strength benefit suspension linkages, exhaust system components, and fasteners.
The aerospace sector has been using CNC machining for titanium parts for years, and the automotive industry is now applying similar techniques to enhance durability while reducing weight.
Machining heat-resistant superalloys, such as Inconel and stainless steel variants, also requires adaptive cutting strategies that balance material removal rates with tool longevity. CNC systems with real-time monitoring adjust cutting speeds and cooling methods to prevent defects and ensure high-quality finishes. These advancements allow modern vehicles to use high-performance materials while staying efficient and cost-effective.
Hybrid CNC Processes
Hybrid manufacturing, which combines CNC machining and additive manufacturing, is changing automotive component production. This method uses the versatility of 3D printing with the precision of CNC machining, enabling manufacturers to create nearly finished parts with additive processes before perfecting them with CNC cutting.
Hybrid CNC machining cuts back on material waste by starting with 3D-printed preforms and refining them with precision cutting. This process minimizes excess material removal and delivers exact tolerances for intricate parts like custom brackets, cooling channels, and lightweight reinforcements.
It also speeds up prototyping and production, allowing engineers to test new designs faster without the delays of traditional tooling. This is a game-changer for the EV industry, where manufacturers constantly refine battery housings, cooling systems, and structural components to meet evolving safety and performance demands.
By combining advanced materials with state-of-the-art machining, the automotive industry is pushing the limits of performance, efficiency, and sustainability. CNC machining drives innovation, turning even the most complex materials into high-performance components.
Quality Assurance and Inspection
Precision is essential in CNC machining, and quality checks ensure every part meets top-notch performance and safety standards. With advanced inspection methods, manufacturers catch even the tiniest flaws before assembly, guaranteeing that each vehicle is built to last.
In-Process Monitoring
CNC machining uses real-time monitoring and adaptive controls, letting operators track progress and spot deviations. On-machine probing keeps parts within tolerance during production.
Constant feedback helps
maintain precision and reduce errors, while adaptive controls adjust the machining process automatically, keeping quality consistent across large production runs.
By keeping engine blocks and suspension components within strict automotive standards, CNC machining improves production efficiency and makes it easier to scale manufacturing without compromising quality.
Post-Production Testing
Manufacturers perform post-production tests to confirm that components meet the necessary specifications. They frequently evaluate critical parts using coordinate measuring machines (CMMs), X-ray inspections, and ultrasonic testing, which can detect cracks, voids, or other hidden defects.
CMMs, for example, take highly accurate 3D measurements to check dimensions and ensure parts fit together. X-ray and ultrasonic testing are valuable for inspecting components like brake callipers and engine parts for internal flaws that could affect performance or safety.
Not everything is automated. There are still visual inspections to check for cosmetic issues, surface finish quality, and appearance. Manufacturers rigorously test every part to prevent defects from reaching the final assembly line.
Compliance with Industry Standards
CNC machining is tightly regulated in the automotive industry to ensure safety and performance. Certifications like ISO/TS verify that manufacturers meet high standards for quality and precision and meet OEM expectations and legal requirements, guaranteeing reliable performance in high-stakes applications.
Automotive manufacturers must ensure parts from different batches fit and perform identically. CNC machining’s repeatability keeps this process consistent, reducing the risk of errors that could jeopardize safety.
How CNC Machining Powers the Next Generation of Automotive Innovation
The demand for advanced automotive components is rising, and CNC machining is driving that evolution, crafting everything from the tiniest gears to the most complex suspension systems. Its precision delivers the performance, safety, and innovation that drivers and manufacturers rely on.
Looking ahead, CNC machining’s ability to tackle increasingly intricate designs and cutting-edge materials unlocks endless possibilities for breakthroughs in automotive technology. The future of car manufacturing? It’s all CNC-machined.
Driving Automotive Innovation with GN’s CNC Machining Solutions
At GN, we’re proud to be a leader and Tier 1 supplier in the automotive industry. We specialize in precision CNC machining services that meet the industry's changing needs. Our full range of manufacturing capabilities includes advanced 5-axis and 9-axis CNC machining, welding, protective coating, heat treating, and assembly, all aimed at delivering top-quality automotive components.
What sets us apart is our GN 4.0 platform, a data-driven solution that uses machine learning and automation to enhance production efficiency and precision. With advanced technology at our core, we don’t just meet industry standards — we surpass expectations in quality and performance.
By partnering with us, automotive manufacturers gain a vertically integrated supplier dedicated to innovation, quality, and efficiency that will help them stay ahead in an ever-evolving industry.
Reach out today to learn more about the GN advantage.