Predictive Maintenance: Avoiding Unplanned Manufacturing Downtime with AI Insights
What if you could stop problems before they occur? While this was once the realm of science fiction, predictive maintenance makes it a reality.
Equipment failures lead to production halts, increased maintenance costs, and lost revenue. Traditional maintenance approaches that rely on reactive and preventive strategies fail to minimize these issues.
Now, AI-powered predictive maintenance transforms maintenance processes by detecting potential failures before they occur. This proactive approach allows manufacturers to optimize efficiency, extend equipment lifespan, and ensure smooth operations.
Today, we’ll break down some moving pieces that make predictive maintenance possible. Keep reading to learn how upgrading your systems or choosing the right partner can increase production quality.
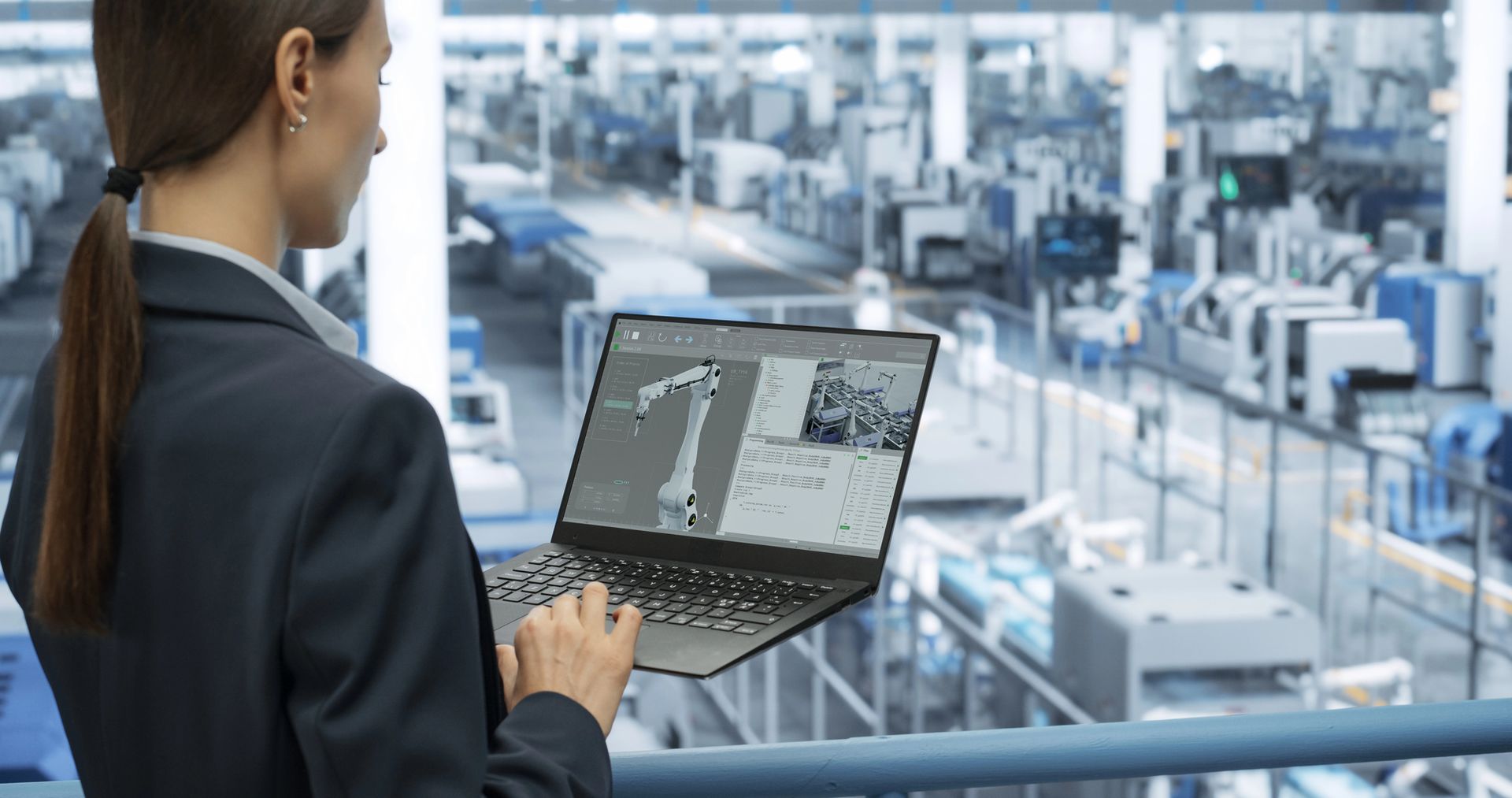
Understanding Predictive Maintenance in the Smart Factory Environment
Smart factories aren’t simply a trending term, they’re a major shift in how we approach manufacturing. Predictive maintenance is one of the major processes involved that make smart factories so valuable — let’s explore how smart factories leverage predictive maintenance.
Defining Predictive Maintenance
Predictive maintenance leverages AI-driven data analysis to forecast equipment failures before they lead to unplanned downtime.
How does traditional reactive or preventive maintenance compare to predictive maintenance? These legacy methods rely on scheduling services regardless of their real-world condition.
Conversely, predictive maintenance strategies use real-time monitoring alongside historical data to anticipate issues.
Role of GN’s Smart Factory
We’ve fully embraced Industry 4.0 with our GN 4.0 platform, which integrates IoT sensors, AI-driven analytics, and cloud computing into its manufacturing processes.
This intelligent system enhances operational efficiency by continuously monitoring machine conditions and predicting failures before they occur.
Impact on Efficiency
Well-planned maintenance translates to consistent uptime, stable production schedules, and lower operational costs. You’ll avoid costly unplanned downtime while maximizing planned downtime to have a minimal impact on production.
Extending the lifespan of your equipment goes far beyond cutting costs. You’ll also delay needing to replace equipment, which can have a noticeable impact on efficiency for larger operations.
The AI/IoT Connection: Gathering and Analyzing Data
AI and the Industrial Internet of Things (IoT) work together to enable predictive maintenance capabilities. You’ll need data, the right models, and processing power — let’s explore each of these aspects.
Key Data Inputs
Predictive maintenance depends on data, embedded sensors and IoT devices provide this valuable data. Sensors or metrics that are most relevant include:
- Vibration analysis detects imbalances or misalignments in rotating components.
- Temperature monitoring identifies overheating issues before they cause damage.
- Acoustic signals analyze sound patterns to detect wear and tear.
- Power consumption and unusual energy usage can indicate inefficiencies or impending failures.
Here at GN, our IoT network gathers and transmits this data continuously, which creates a foundation for AI-driven insights.
Data Processing and Machine Learning Models
Machine learning models trained to provide predictive maintenance schedules are at the heart of this powerful new utility. Accurate data capture is the first step, and from there, ML models are able to produce actionable insights.
GN 4.0 processes vast amounts of sensor data in real time. Our AI models are trained on historical data to identify deviations from normal operation patterns and flag early warning signs. This utility enables predictive interventions before failures escalate.
Key Components of a Predictive Maintenance Strategy
Correctly implementing a predictive maintenance strategy requires having a few key components in place. Each of them plays an important role in producing accurate, valuable predictive maintenance schedules — let’s break them down.
Condition Monitoring
Real-time machine health monitoring enables deep operational insights. Sensors continuously stream data, while AI algorithms assess performance and provide actionable alerts when maintenance is necessary.
Data Storage and Analysis
A robust data infrastructure is crucial for predictive maintenance success. GN 4.0 employs secure cloud and edge computing solutions to efficiently handle vast sensor data, unlocking fast and reliable analysis.
AI Algorithms & Modeling
Machine learning models leverage historical trends, anomaly detection, and predictive modelling to foresee potential failures. For example, subtle shifts in a CNC machine’s acoustic profile may indicate a bearing failure, allowing timely interventions before catastrophic damage occurs.
Maintenance Scheduling and Execution
AI-driven alerts enable maintenance teams to schedule repairs proactively, minimizing disruptions. These schedules lead to better resource planning, optimized labour allocation, and reduced overall costs.
Benefits: Minimizing Downtime, Maximizing Efficiency
We’ve seen the shift from static, time-based maintenance to dynamic, condition-based interventions. What benefits does this shift bring to the operation? A few of the top benefits are:
- Reduced unplanned downtime: Predictive maintenance drastically reduces unexpected outages. Determinative maintenance cuts ensure consistent production schedules and operational stability.
- Optimized asset utilization: Healthy machines operate at peak efficiency, enhancing throughput. Improved equipment reliability also simplifies scheduling and inventory management.
- Extended equipment lifespan: Proactive maintenance prevents excessive wear and damage, extending machinery lifespan. This reduces capital expenditures and promotes sustainable operations by minimizing material waste.
- Enhanced safety and compliance: Well-maintained equipment reduces workplace hazards and ensures compliance with industry regulations, improving overall safety and operational integrity. A safe work environment significantly improves job satisfaction by reducing injuries.
Potential Challenges and How to Overcome Them
Any significant change in manufacturing brings entirely new challenges and hurdles. Fortunately, anticipating hurdles is necessary to overcome them, so let’s explore what to expect on the horizon.
Data Quality and Sensor Calibration
Accurate and consistent data is critical for reliable predictions. Regular sensor audits and calibration schedules ensure high-quality data inputs, reducing the risk of false alarms or missed failures.
Sensors and IoT devices should be regularly inspected to ensure that the data being captured is accurate. The process doesn’t end at initial deployment but requires ongoing inspections.
Model Complexity and “Black Box” Concerns
AI-driven maintenance models can be difficult to interpret as they don’t operate like a traditional program. Identifying and isolating issues that affect results can be highly challenging.
GN employs explainable AI tools and simplified models where appropriate to enhance transparency, helping maintenance teams trust and act on AI-generated insights.
Cultural Shift and Employee Buy-In
Moving away from traditional maintenance approaches to predictive strategies requires organizational change. Prioritizing clear communication about benefits, management support, and hands-on training can help employees embrace AI-driven maintenance processes.
Additionally, provide plenty of training and information about how these new tools will be used to augment, not replace, their jobs.
Future of Predictive Maintenance and AI-Driven Manufacturing
How might future and emerging technologies change predictive capabilities? We are fully evolving technologies to become increasingly powerful for enabling valuable predictive capabilities.
A few advances we expect to make predictive maintenance even more valuable include:
- Adaptive AI: Advanced AI models will continuously refine themselves based on new data, enhancing predictive accuracy and optimizing interventions. Models need to be capable of producing increasingly valuable results.
- 5G and edge computing: Integrating 5G networks and edge computing will enable real-time processing of sensor data, reducing latency and enhancing predictive maintenance effectiveness.
- Integration with digital twins: Digital twins are virtual replicas of physical assets and will allow manufacturers to simulate maintenance scenarios, test AI-driven strategies, and optimize decision-making without disrupting operations.
- Global manufacturing ecosystem: As predictive maintenance becomes more widespread, manufacturers will benefit from shared AI insights, industry-wide benchmarks, and collaborative advancements in maintenance strategies.
Predictive Maintenance Requires the Right Technologies
Predictive maintenance, powered by AI and IoT, is transforming the manufacturing landscape. Manufacturers need to update their systems or choose partners who already leverage the latest tech to enhance operations.
By proactively identifying potential failures, GN ensures minimal downtime, optimized efficiency, and extended equipment longevity. Is it time to implement predictive maintenance or work with someone who already has?
Contact us today to learn how we can help.