The Ultimate Guide to 5-Axis CNC Machining: Precision and Efficiency for Modern Manufacturing
5-axis CNC machining can help manufacturers tackle complex designs by combining precision and efficiency to deliver exceptional results.
Keep reading to learn how 5-axis CNC machining outperforms traditional methods, benefits industries like aerospace and automotive, drives innovation through real-world applications, and positions GN as a leader in advanced manufacturing.
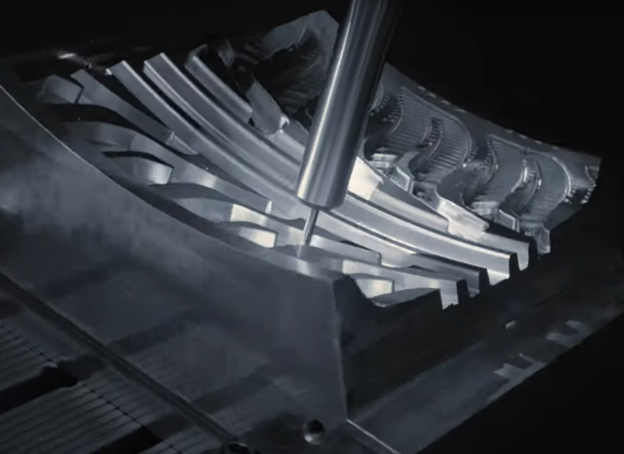
What is 5-Axis CNC Machining?
5-axis CNC machining is a state-of-the-art manufacturing process that allows cutting tools to move across five axes simultaneously. Unlike traditional methods, this system includes three standard linear axes and two rotational axes.
These additional movements create complex geometries with unmatched precision and efficiency. By removing multiple setups, manufacturers can enjoy seamless workflows and produce consistent results, even for intricate designs.
Comparison with 3-Axis and 4-Axis CNC Machining
While 3-axis machining handles more straightforward tasks by operating along X, Y, and Z axes, it struggles with multi-sided machining. 4-axis systems add rotational movement along one axis, enabling better handling of cylindrical objects.
5-axis machining surpasses both by tilting and rotating simultaneously. This capability minimizes repositioning, reduces errors, and accommodates more sophisticated parts, making it a game-changer for high-stakes industries like aerospace and defense.
Explanation of the Five Axes
The five axes in this system include the three linear ones (X, Y, Z), used for standard forward-backward, side-to-side, and up-down movements. The additional rotational axes — commonly called A and B — enable tilting and rotation of the tool or workpiece. This flexibility ensures precise machining of intricate angles, curves, and features, even on hard-to-reach surfaces.
Key Benefits of 5-Axis CNC Machining
5-Axis CNC machining is a modern advancement in manufacturing. It solves complex challenges with precision, efficiency, and adaptability. Below are some advantages and practical applications:
Precision and Accuracy
One of the most significant benefits of 5-axis CNC machining is its precision. This technology can achieve tolerances as tight as ±0.0002 inches (0.00508mm), making it indispensable for industries needing flawless components, such as aerospace and medical manufacturing.
The continuous movement across all five axes provides precise tool positioning and reduces errors caused by manual intervention or multiple setups. Its accuracy meets high-performance standards and minimizes material waste, saving on costs and resources.
Reduced Setup Time
A key advantage of 5-axis machining is its ability to work on complex parts in one setup. Unlike 3-axis or 4-axis systems, which often require repositioning the workpiece multiple times (leading to extra time and risking alignment issues), 5-axis technology can reach all sides without manual adjustments.
GN efficiently produces turbine blades and impellers, reducing production time and ensuring fast delivery to clients. This streamlined process empowers manufacturers to meet tight deadlines without compromising quality.
Enhanced Surface Finishes
Another advantage is the superior surface finishes from continuous cutting. Unlike traditional systems, which can leave tool marks from stopping and restarting, 5-axis machining produces smoother transitions and eliminates excessive polishing or grinding.
Components with curved or intricate surfaces, such as medical implants or engine housings, benefit from this capability. For GN, producing parts with minimal post-processing requirements translates to cost savings for their clients while maintaining the highest quality.
Design Flexibility
5-axis CNC machining opens new possibilities for innovative designs. Manufacturers can make components with intricate geometries, undercuts, or unconventional shapes that were once unimaginable, encouraging creativity and allowing manufacturers to address the ever-evolving demands of changing industries.
Applications of 5-Axis CNC Machining
5-Axis CNC machining is transforming modern manufacturing by creating exact and complex parts for the following industries:
Aerospace
The aerospace industry relies on exact parts, such as engine housings, landing gear components, and structural elements, to endure extreme pressures and temperatures. 5-axis machining creates lightweight, durable parts with complex shapes that meet these demanding requirements.
Take titanium turbine blades, for example. With this technology, manufacturers can build them with the perfect amount of strength and lightness. The result? Enhanced aircraft safety and efficiency, even in the toughest conditions.
Automotive
In the automotive sector, 5-axis CNC machining helps create components like engine blocks, suspension parts, transmission housings, cylinder heads, turbochargers, and intricate dashboard components. These parts require tight tolerances to function effectively under constant stress.
This technology can also prototype and produce components for electric vehicles, helping automakers stay ahead in innovation and sustainability.
Defense
Defense manufacturing involves creating components for critical systems such as tanks, guns, missiles, and armoured vehicles. These parts must meet strict specifications for durability and performance in extreme environments.
For example, precision-guided missile systems need components machined to exact tolerances to ensure accuracy. The ability of 5-axis machining to handle complex geometries makes it indispensable for the
defense sector.
Oil and Gas
Oil and gas operations require parts such as drill bits, impellers, valve bodies, and casing components to withstand corrosive, abrasive, high-pressure, and extreme temperature environments.
5-axis machining ensures the manufacturing of these components are to exact specifications, minimizing downtime during operations. For example, impellers with precise blade angles improve fluid movement in pipelines and pumps.
Technology
In the technology industry, 5-axis machining can create advanced components like microchips, robotic parts, medical devices, and wearable tech. Its precision makes it possible to produce intricate designs for cutting-edge tools like semiconductor manufacturing equipment.
For example, robotic arms used in factories or surgery rely on this technology to achieve the exactness required for smooth and reliable performance. Similarly, medical implants, like custom-fit joint replacements, benefit from 5-axis machining’s ability to deliver flawless precision and functionality.
How GN Utilizes 5-Axis CNC Machining
GN utilizes advanced 5-axis CNC machining to create high-quality, intricate components for many industries. Their commitment to accuracy, efficiency, customer satisfaction, and innovation shows at every production stage.
One standout feature is their rigorous quality control. By using cutting-edge 5-axis CNC machines, they consistently manufacture parts that meet even the most demanding standards for detail and reliability.
Timely delivery is also a priority. With 5-axis technology, they require fewer setups, streamlining the production process and reducing turnaround times.
GN reinforces their dedication to quality with industry-recognized certifications, including:
- AS9100D
- ISO 9001:2015
- ISO 45001:2018
- ISO 14001:2015
- CWB CSA Standard W47.1
- Controlled Goods Program
The Future of 5-Axis CNC Machining
The future of 5-axis CNC machining will combine innovation and sustainability. Trends like automation, artificial intelligence (AI), and hybrid manufacturing are transforming what this technology can do.
Automation simplifies machining by reducing human involvement and cutting down errors. AI makes machines smarter, helping them adapt to challenges and make better decisions. For example, AI can fine-tune tool paths, predict maintenance, and improve efficiency.
Hybrid manufacturing, which merges additive (3D printing) and subtractive (traditional machining) methods, creates new possibilities for creating complex parts that weren’t feasible before.
GN stays ahead of these advancements by investing in the latest technology and research. This forward-thinking approach helps them exceed client needs while keeping up with industry changes.
Sustainability is also a big part of the future. As industries aim to lower their environmental impact, 5-axis CNC machining is evolving to help. By reducing material waste and supporting eco-friendly materials, this technology plays a key role in greener manufacturing.
Experience the GN Advantage Yourself
At GN, we integrate advanced technology and commitment to client satisfaction to deliver outstanding solutions.
Adopting the latest advancements in 5-axis CNC machining and prioritizing sustainability demonstrates our dedication to staying ahead of industry trends.
When precision and innovation are non-negotiable, we’re your trusted partner in 5-axis CNC machining. We work closely with every client to ensure we tailor every component to exact requirements. Our focus on communication and responsive service builds long-term partnerships and ensures we exceed customer needs at every level.