Sustainable Solutions: Leveraging Industry 4.0 Innovations for Eco-Friendly Manufacturing
Sustainable Solutions: Leveraging Industry 4.0 Innovations for Eco-Friendly Manufacturing
Sustainability is a major focus across all industries as world governments and corporations dedicate themselves to fostering a cleaner environment and enhancing energy efficiency. Computer Numerical Control (CNC) machining and its supporting technologies have opened up a new frontier of eco-friendly and economically viable manufacturing.
Known as Industry 4.0,
manufacturing is leading the charge toward sustainability, automation, and a higher quality of end products. Supporting technologies like AI and IoT allow for a new level of efficiency in energy usage and beyond.
Choosing sustainable manufacturing practices helps your company contribute positively to the environment, improving both your reputation and the sustainability of the end product. A new level of precision also allows for unprecedented durability and reliability.
So, keep reading as we explain how you can adopt sustainable practices with high-quality results by choosing the leading-edge CNC industry.
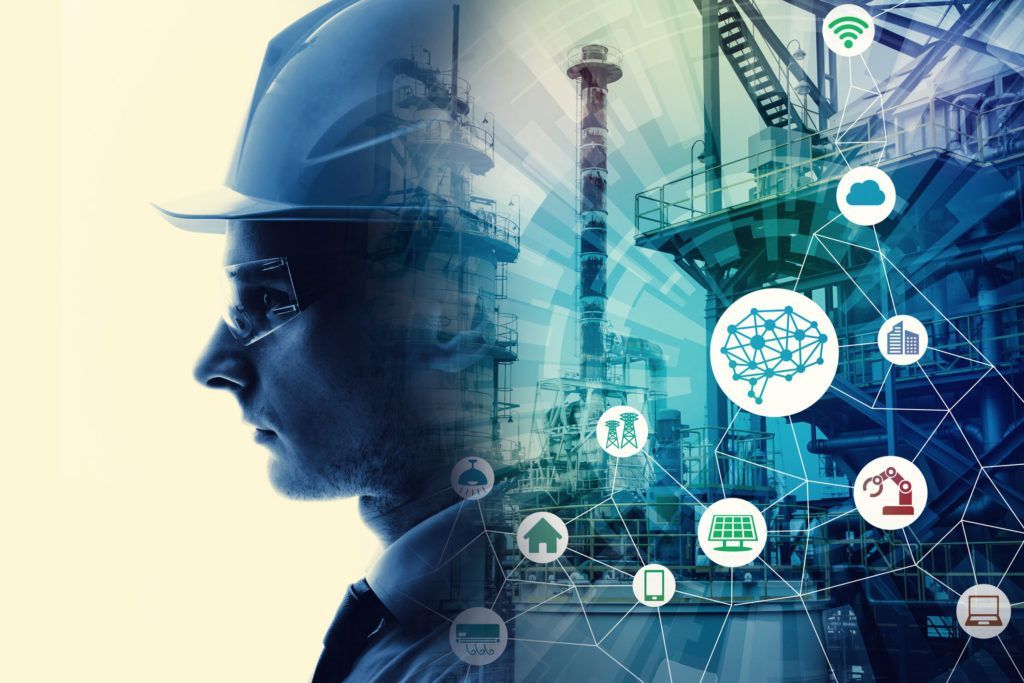
Understanding Industry 4.0 in Manufacturing
Industry 4.0 is the Fourth Industrial Revolution that leverages new and emerging technologies, such as the Internet of Things (IoT), Artificial Intelligence (AI), and Big Data.
In the CNC machining process, these technologies enable streamlined operations by enabling real-time monitoring, predictive maintenance, and efficient resource management. Combined, these technologies reduce costly downtime, material waste, and energy consumption—foundational concepts of sustainability.
The Pillars of Sustainability in Manufacturing
What is sustainability in the manufacturing sector? The pillars of sustainable manufacturing processes demonstrate the overarching initiatives necessary, which are:
- Economic Viability: Maintaining profitability and achieving positive returns from investments in technology, people, and processes.
- Environmental Responsibility: Implementing energy-efficient manufacturing equipment and processes to promote a cleaner environment.
- Purpose-Driven People: Fostering an equal opportunity environment as an employer, valuing diversity in work and life experiences, cultivating passionate and engaged employees through comprehensive training opportunities.
Even though it may seem like a challenging balance, the technologies available can significantly contribute to it. Industry 4.0 enables efficient production with minimal environmental costs while providing safe working conditions.
Additionally,
enhancing the energy efficiency
of your manufacturing processes also helps local communities, further contributing to the social dimension of sustainability.
Leveraging Industry 4.0 for Eco-Friendly Manufacturing
The rise of Industry 4.0 and widespread digital transformation has led to significant cultural and operational changes within manufacturing. The seamless integration of people, data, and assets has also resulted in new optimizations. Here are a few examples showing how Industry 4.0 solutions are revolutionizing efficiency, visibility, and sustainability within manufacturing and supply chains:
- Collaborative Design Platforms: Industry 4.0 allows for the creation of collaborative design platforms, enabling R&D teams, product designers, and stakeholders from all corners of your organization to access and contribute to design data and insights. This inclusive approach fosters cross-functional collaboration, facilitates idea sharing and knowledge exchange, resulting in well-informed design decisions and expedited development of innovative, customer-centric products.
- Predictive Maintenance: By harnessing IoT sensors and data analytics, manufacturing enterprises can monitor equipment health in real-time. Predictive maintenance algorithms preempt potential failures, enabling the implementation of proactive processes that can slash downtime by up to 50% and extend asset lifespan by as much as 40%.
- Supply Chain Optimization: Industry 4.0 enables end-to-end visibility across your global supply chain. Real-time data from suppliers, inventory levels, production schedules, customer demand, internal teams, and other sources empower you to optimize logistics, harmonize supply and demand, enhance order fulfillment, and elevate overall supply chain and manufacturing efficiency.
- Agile Manufacturing: AI and advanced analytics empower you to gather and analyze real-time customer insights and feedback from diverse sources such as social media, online reviews, and customer support interactions. Leveraging this data, your R&D teams and product designers can pinpoint consumer preferences, pain points, and emerging trends. Incorporating this feedback into the design process facilitates the swift development of products that resonate with market demands, enhancing satisfaction, fostering loyalty, and propelling innovation.
- Quality Control and Defect Detection: By leveraging IoT devices and machine learning algorithms, you can collect real-time data from all your production lines. Continuous monitoring of the manufacturing and production process enables the prompt detection of anomalies, identification of quality issues, and implementation of corrective measures, ensuring stringent product quality standards.
- Circular Economy Practices: Industry 4.0 facilitates the adoption of circular economy principles, emphasizing waste reduction and maximizing the reuse, refurbishment, and recycling of materials. Through the utilization of Big Data analytics and IoT networks, you can track product lifecycles, establish reverse logistics for product returns, and optimize the recovery of valuable resources. Additionally, AI-powered advanced analytics empower product designers to develop inherently sustainable products, designed from inception to minimize resource consumption and facilitate easier recycling or repurposing.
Manufacturing leverages these technologies in real-time and throughout the equipment’s lifecycle to create precise, sustainable, and durable results.
Challenges and Solutions in Adopting Industry 4.0
Adopting Industry 4.0 for your in-house processes is no small initiative. It’s a new wave of technologies and specialized applications, creating new challenges that must be solved before you can start reaping the benefits.
So, let’s break down challenges in the CNC industry and overall sustainability practices that won’t always be an easy fix but do have a solution:
- Upfront investments: Implementing new technologies often requires new physical equipment or specialized software. Tackle this challenge by starting with smaller applications, scaling up, and applying what you’ve learned to the next project. Don’t make the mistake of trying to do everything at once.
- Skilled personnel: Industry 4.0 brings a new paradigm of manufacturing. Older skills will still be relevant, but newer expertise will be necessary for many roles. Hire or upskill workers in data analysis, IoT management, and AI. While challenging, it’s a necessity that can be planned for as you migrate.
- Complexity retrofitting older machines: Not every process will need brand-new equipment to become a sustainable manufacturing process. You may be able to retrofit older machines with newer equipment, like IoT devices, but it can be challenging. Explore specialized methods for upgrading your machines; you can benefit from existing solutions rather than finding new ones.
Future of Sustainable Manufacturing Industry
Nobody knows what the future holds, but we can make an informed projection about the future of sustainable manufacturing.
There is a growing emphasis on companies making significant, noticeable steps towards
positive stewardship of the environment. Leveraging sustainable industrial manufacturing processes is a significant step in the right direction.
Over the next decade or so, we may see additional regulatory pressure and consumer demand for products that use sustainable practices.
At the same time, the technologies behind Industry 4.0 will continue to evolve. AI has advanced rapidly in the past two years and is now a major industry. Advanced sensors will make IoT devices more accurate and valuable, while Big Data leverages IoT data for widespread transformation.
Migrating to sustainable practices in-house and choosing partners who are doing the same will go a long way toward preparing your organization for the rapidly changing future.
Getting Started with Industry 4.0
Manufacturers looking to upgrade their in-house processes may face new challenges, but it’s worth the investment in creating a sustainable and cost-effective future for your company. Let’s explore a brief overview of how you can adopt Industry 4.0:
- Conduct an audit of your current processes and equipment. Identify specific areas that are using outdated or resource-intensive technologies.
- Set clear, achievable goals for migrating to Industry 4.0. Don’t only set long-term goals; make short-term ones as well. Keep the focus on sustainability rather than profitability only.
- Explore any possible funding options from government grants. Several governments have established grants or other incentives for sustainability efforts, reducing initial investment.
- Create a plan for phased adoption that begins with pilot projects. These projects will allow you to fine-tune the technologies used and then start scaling up.
- Invest in plans to upskill your workforce, hire new specialists, and develop ongoing training programs to stay on top of new changes in the technologies you adopt.
- Once initiatives are scaled up and implemented, create plans for continuous improvement by evaluating performance and other metrics. Similarly, consistently make an effort to stay aware of any changes in the technologies behind your processes.
These steps will help you transform manufacturing processes and any other workflows that need a sustainability overhaul. Additionally, choose vendors and partners committed to sustainability, as their
environmental stewardship will be reflected in your own
contributions.
Benefit from Sustainable Manufacturing Technology with GN
Embracing the global push for sustainability with Industry 4.0 also helps your company cut costs, improve production quality, and protect local communities. The technologies behind the latest Industrial revolution have allowed manufacturing to be hyper-efficient without increasing costs, a win for you and the environment.
Explore how to integrate these technologies as a strategic asset as you move towards sustainability. Partnering with the right machining partner helps you immediately start benefiting from these next-gen technologies so you can focus on ways to apply them in other areas of operations.
GN is an industry leader in Industry 4.0. We’ve developed
GN 4.0 to transform our existing services with these transformative technologies and help our partners reap the rewards of everything they have to offer.
Ready to enhance your sustainability efforts in a way that also boosts product quality?
Reach out to us today to learn more about our processes.
Sources:https://www.sap.com/canada/products/scm/industry-4-0/what-is-industry-4-0.html#