Key Benefits of Smart Manufacturing: Enhancing Efficiency and Quality in Production
To stay ahead in an increasingly competitive market, manufacturers must constantly find new ways to produce the highest-quality products at the lowest cost. That's where smart manufacturing comes in. By combining artificial intelligence, the Internet of Things, data science and robotics, manufacturers can optimize efficiency, reduce errors, and maximize equipment uptime while also improving sustainability, product quality, and agility.
Today, we're going to explore how a smart factory makes all those things possible.
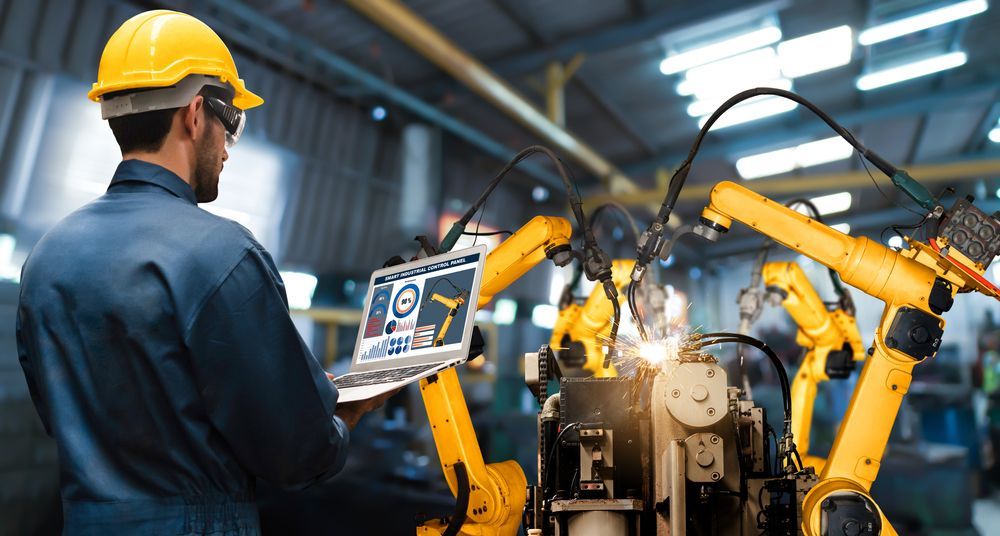
Enhancing Efficiency with Smart Manufacturing
According to McKinsey, up to 87% of production tasks can potentially be offloaded to machines. In addition to reducing costs, combining automation with today's sophisticated robotics technology has the potential to considerably streamline production processes. Industrial machines can work faster than humans, don't get tired, and don't make mistakes.
Human operators, meanwhile, can redirect their attention to more complex and intricate tasks with which robots may struggle.
Equipment failure is another major efficiency-killer in manufacturing. This can be addressed through a combination of smart sensors, cloud-based monitoring tools, and AI-driven analytics. Let's say a component is running at a slightly higher temperature than usual.
You could detect that temperature increase immediately and flag the component to be swapped out, avoiding equipment failure and potentially costly downtime.
Improving Quality with Smart Manufacturing
Computer Numerical Control (CNC) machining has been a cornerstone of the manufacturing industry for decades. By using pre-programmed computer software, manufacturers can control and automate the movement of a wide range of complex machinery, ensuring a high level of accuracy. This is especially valuable for precision parts production, where even the smallest defect or deviation will ruin a product.
By incorporating AI into CNC machining, you can automate considerably more complex tasks. They can also enable continuous production through AI-driven robots. These robots work with flawless precision, ensuring accuracy and uniformity even as they work around the clock.
AI and machine learning are also invaluable for quality control and defect detection. Traditionally, these processes are either completely manual or supported by limited rule-based automation. They also happen at scheduled intervals, making them a massive efficiency bottleneck.
With AI, quality control processes can happen in real-time and without interrupting production. Through machine learning, an algorithm can be trained to recognize anomalies that may indicate a defect. Because this process can happen throughout production it can also identify defective components immediately, ensuring that you aren't wasting resources pushing through faulty products.
This doesn't just apply to products, either. You can also use AI to identify an element of your production line that's performing abnormally. This process, known as anomalous cycle detection, is basically like defect detection but for systems and processes rather than products.
As you continue to monitor your production line, you'll also find that machine learning allows the algorithm to become gradually more accurate and effective. Eventually, you may see defect detection rates increase by up to 90%. This high rate of detection combined with the accuracy of technologies like AI-powered CNC helps to ensure consistent uniformity and product quality.
The Role of Data Analytics in Smart Manufacturing
In many ways, information is the lifeblood of modern manufacturing. But the sheer volume of information generated by even a small-scale factory would overwhelm even the most seasoned human analyst. That's why data analytics is so crucial.
Using a purpose-built platform, a manufacturer can orchestrate data from multiple sources and then use that data to make more informed production decisions. We already mentioned predictive maintenance earlier. It's far from the only way manufacturers can combine analytics and AI.
You can use performance insights to learn more about production efficiency, for instance. This allows you to eliminate shortfalls, streamline processes, and improve resource utilization. Predictive analytics comes into play here, helping to identify potential areas of improvement and allowing you to make more informed decisions about process optimization.
There's also digital twinning, a technique which involves making a virtual replica of your processes and products and then running it through multiple real-time simulations. Leveraging a combination of AI and analytics, you can test and optimize as much as necessary. BMW Group even went so far as virtualizing an entire factory to use as a testbed for potential process improvements.
Finally, demand forecasting gives you advanced warning of emerging trends and possible disruptions. You can then adjust your production schedules accordingly. As we'll explain in the next section, this is incredibly important if you want to remain agile and adaptable.
Additional Benefits of Smart Manufacturing
Before we wrap things up, there are a few other benefits that are worth mentioning.
Flexibility and Scalability
Technology moves fast. Just look at how quickly multiple industries embraced generative AI after ChatGPT was released a little over a year-and-a-half ago. To remain competitive, you need flexible and scalable production that you can easily adapt to changing market demands.
Smart manufacturing technologies help this happen in a few ways.
First, you've got complete visibility into and control over your manufacturing processes and supply chain. This means that you can quickly pivot and adapt in response to market changes. What's more, predictive analytics can provide you with prior warning of those changes, allowing you to prepare in advance.
The increased production efficiency and accuracy enabled by smart manufacturing are also hugely beneficial here. Your processes remain consistent at virtually any scale. This means that you can increase or reduce production in response to demand without much difficulty.
Sustainability
Through smart manufacturing, you'll have a complete picture of each stage of your product's lifecycle. You can use that information to not only reduce energy usage and waste production, but also to design more sustainable products. Strategic initiatives aside, smart manufacturing technology can make you more sustainable in several other ways, as well:
- Automatically controlling and optimizing energy consumption.
- Avoiding overproduction through demand forecasting to reduce material waste.
- Limiting carbon production through the use of industrial robots.
- Automated air quality monitoring.
- Automated handling of hazardous materials.
Employee Empowerment
There's one thing a lot of people seem to forget amidst the hype of Industry 4.0: Without people, none of these sophisticated technologies or promising innovations mean anything. You need human intelligence to guide machine intelligence. You need human ingenuity, creativity, and intuition to experience the true potential of smart manufacturing.
In the same vein, smart manufacturing also empowers human operators, providing them with advanced tools and real-time insights that make them able to work more efficiently and effectively. Your people can make faster, more informed decisions, break down data silos for better communication and collaboration, and focus on high-value activities rather than mundane work. That means they'll be more satisfied with their work, more loyal to your company, and ultimately, more productive.
Embrace Smarter Manufacturing with GN Corporation
Success in the manufacturing sector means finding the most efficient way to produce the highest-quality products. With smart manufacturing, that's now easier than ever to achieve. By combining technologies like artificial intelligence, analytics, the Internet of Things, and sophisticated robotics, manufacturers can operate faster, more efficiently, and at a larger scale while also ensuring consistent product quality.
GN Corporation understands this. It's why we've not only embraced Industry 4.0, but done so in a way that empowers both our people and our clients. And it's why we fully intend to continue growing and evolving alongside the manufacturing sector.
Smart manufacturing is the future — let us show you how to embrace it.
Partner with us to
learn more about GN 4.0 and how our smart factories can help you improve product quality, increase production efficiency, and reduce overhead.