A Deep Dive Into CNC Machining Quality Control and Inspection
CNC machining has rapidly become the go-to option for industries that require durable end products that meet strict design specifications and quality standards. Aerospace, oil and gas, automotive, and defense industries benefit from CNC production machining.
Quality machine services can take complex designs and manufacture defect-free products, but having the right quality control and inspection processes is necessary to make the most of CNC machining.
What does it take to improve quality control in CNC machining to deliver exceptional precision in manufacturing? Keep reading to learn more about these processes and how to enhance them.
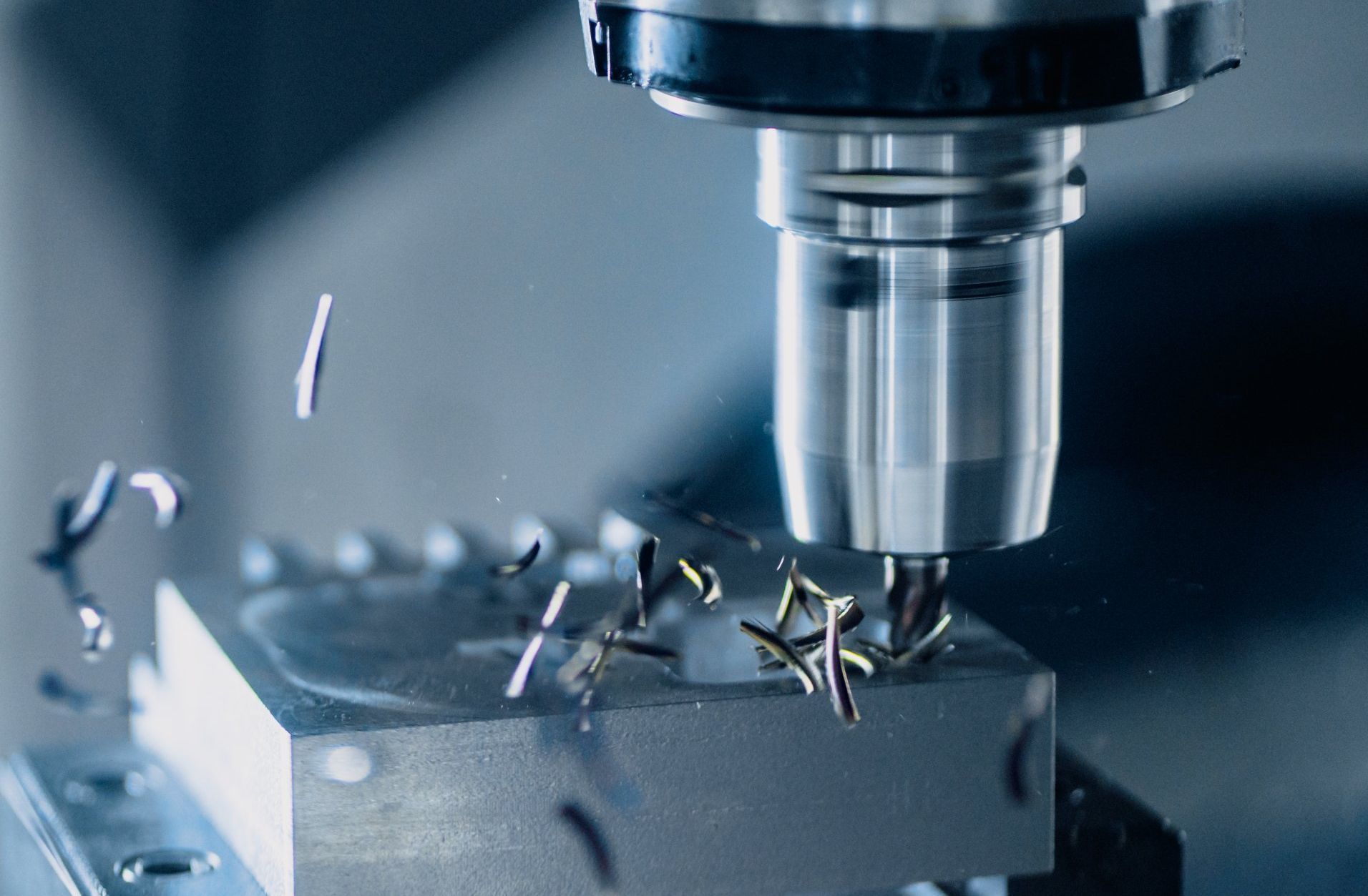
Brief Overview of CNC Machine Quality Control and CNC Inspection
Quality control and CNC inspections play a crucial role in ensuring CNC machining and manufacturing produce goods that meet specifications and expectations.
Quality control aims to identify deviations from set standards using precision measuring instruments and advanced techniques. CNC inspection processes are a systematic procedure to ensure parts meet specified standards.
So, let’s quickly go over a high-level overview of the process:
- The manufacturing process begins with pre-machining inspections that assess raw materials and tool conditions.
- During machining, periodic checks monitor accuracy and tool wear.
- Once a machining job is complete, final inspections measure dimensions, surface finish, and other vital parameters using tools like micrometers, calipers, and coordinate measuring machines (CMMs).
- Any discrepancies identified will require corrective actions to ensure a consistent and high-quality output.
Quality Control vs. Quality Assurance in Manufacturing
Quality control and quality assurance are used interchangeably, but they address quality from different perspectives. It’s worth quickly exploring these perspectives before diving deeper into quality control.
Quality Control (QC) is product-oriented and focuses on testing the output to ensure it meets specific standards. It's a reactive approach, identifying and rectifying defects in finished products.
Quality Assurance (QA) is process-oriented and a proactive approach aiming to prevent defects by ensuring that the processes leading to the product's creation are high quality.
QC and QA are integral for a well-rounded approach to quality in manufacturing industry. While QC aims at catching faults in finished products, QA seeks to create an environment where those faults are less likely to arise.
What Are the Key Quality Control Parameters in CNC Machining?
CNC machining depends on computer precision tools that take raw materials to manufacture various parts and components.
The quality of these components is determined by various parameters that ensure they meet specified standards and function as intended. So, let's explore these parameters to learn how they affect the overall CNC machining process.
Dimensional Accuracy and Tolerance
Achieving the correct dimensions is crucial in CNC machining. Even slight deviations can render a part unusable, especially in precision industries such as aerospace or defense. CNC measurement checks in quality control are necessary before using the component in the end product.
Dimensional accuracy and tolerance and cornerstone parameters for quality control — let’s define these terms:
- Dimensional accuracy refers to the degree to which the actual dimensions of the machined part align with the specified dimensions.
- Tolerance is the permissible limit or limits of variation in a particular dimension of a machined part.
Instruments like micrometers, calipers, and coordinate measuring machines (CMM) are employed to gauge dimensional accuracy. Additionally, tool wear and machine calibration can affect the level of precision of a machined component, making inspections crucial to maintain quality.
Surface Finish and Roughness
A part's surface finish can influence its function. Surface finish describes the texture and quality of the machined part's surface.
Surface roughness is a quantitative measure of the fine irregularities on the surface, usually described in microinches or micrometers. Profilometers and surface roughness testers are typically used to measure surface roughness.
The tool's condition, material properties, feed rate, and type of coolant can all play a role in the resulting surface finish.
Material Hardness and Strength
The hardness and strength of a material can impact its suitability for CNC machining and the wear on tools.
- Material hardness indicates a material's resistance to deformation or scratching. Material strength can be determined through tensile, compressive, and shear tests.
- Material strength describes how much force a material can endure without breaking or deforming. Hardness is typically gauged with quality control checks like the Rockwell or Brinell hardness tests.
Using the correct cutting tool and parameters for a particular material's hardness is crucial for efficient machining and quality outcomes.
Techniques and Tools for Quality Control in CNC Manufacturing
How do companies ensure quality control in CNC manufacturing? Let’s explore a few of the standard techniques and tools used in CNC machining services that make sure the end result is of the highest quality.
- Coordinate measuring machines (CMM): These advanced devices measure the geometry of physical objects at discrete points on their surfaces, ensuring parts are machined to precise specifications.
- Optical comparators: These instruments magnify silhouettes of parts onto a screen, allowing for a visual comparison against set standards and templates.
- Surface profilometers: Profilometers are used to measure the surface roughness of a machined part, providing a quantitative analysis of surface textures and ensuring finishes meet provided standards.
- Hardness testers: Instruments that determine a material's resistance to deformation, specifically, its ability to resist scratching or denting, ensuring the machined parts have the requisite strength and durability.
Inspection Methods for CNC Machined Parts
We’ve been primarily looking at quality control, but what inspection methods are used in CNC production? Let’s explore the different CNC inspection equipment and processes that make sure the result meets strict requirements.
- First article inspection: This is the initial step, where the very first part produced in a production run is inspected in detail to ensure it meets all design specifications. It serves as a benchmark for subsequent parts.
- In-process inspection: As production continues, periodic checks are performed on parts at different stages of the machining process. This step ensures consistent quality and allows for immediate corrective actions if deviations are detected.
- Final inspection: Once the CNC machining process is completed, a thorough inspection of the finished parts is conducted to confirm they meet all design and quality standards before being dispatched or assembled.
- Statistical process control (SPC): This method uses statistical tools and techniques to monitor and control the production process. By analyzing data from sample parts, SPC can detect trends or variations that might indicate potential quality issues.
Ensuring Compliance with Industry Standards and Regulations
Meeting industry standards and regulations ensures consistent product quality, safety, and reliability. Compliance builds trust among stakeholders and also mitigates risks associated with manufacturing oversights. Let’s briefly touch on two industry standards CNC machining providers often need to meet.
ISO 9001 Certification
ISO 9001 is a globally recognized quality management system standard. This certification demonstrates a company's commitment to meeting customer demands while abiding by strict regulatory requirements.
AS9100 for Aerospace Industry
AS9100 is a rigorous standard tailored for the aerospace sector. It encompasses ISO 9001's requirements, adding aviation-specific criteria to ensure the highest levels of safety and quality in aerospace manufacturing.
Common Challenges and Solutions in CNC Machining Quality Control
CNC machining quality control requires solving various challenges to machine the specified result. While not an all-inclusive list, let’s review some of the common challenges that need to be addressed with CNC quality control:
- Account for variations in raw materials: Variations in raw materials can lead to inconsistent final products. Additionally, different material grades or slight discrepancies in composition can alter machining behaviors. Sourcing quality materials is crucial to overcome this hurdle.
- Addressing machine and tooling issues: These issues, such as misalignment or wear, can compromise precision. Regular maintenance, calibration, and tool condition monitoring are essential to mitigate these concerns.
- Implementing practical corrective actions: It’s crucial to implement the right corrective actions when necessary, be it adjusting machine parameters, retraining personnel, or refining processes. This addresses the immediate issue and fortifies the production system against future quality lapses.
Another emerging concern in the industry is the integration of automation in CNC processes. As companies venture into "lights out" operations, where machines run without human intervention, the question of quality assurance becomes even more critical. Traditional methods, such as using probes for quality checks, might not always be feasible, especially in setups without dedicated storage for such equipment.
The industry is in dire need of innovative solutions that can seamlessly integrate with automated operations and ensure that every part produced meets the highest standards. This challenge opens the door for machinists and quality control experts to collaborate, innovate, and elevate the standards of CNC machining.
The Role of Personnel and Training in Quality Control
Quality control in CNC machining is not just about sophisticated equipment and advanced technology. Instead, quality control depends on skilled operators and inspectors who play an instrumental role in ensuring that the end products meet strict standards and requirements.
Operators not only operate machinery to its optimal potential but also identify subtle nuances that automated systems might miss. Trained inspectors meticulously scrutinize every product, ensuring that any deviation, no matter how minor, is caught and corrected.
The rapid evolution of technology and changing industry standards make continuous learning necessary. Training programs ensure that the workforce is updated with the latest techniques and tools and instilled with a deep-rooted understanding of quality norms.
Provide up-to-date employee training or use a CNC machining partner with highly trained specialists.
Key Takeaways for CNC Machining Quality Control
Quality control in CNC machining is crucial to producing parts and components that meet strict standards and safety requirements. Let’s recap the key takeaways for any industry looking to enhance its CNC manufacturing quality control processes:
- Invest in training: Give your personnel the latest knowledge and best practices through regular training sessions.
- Prioritize regular maintenance: Ensure machines and tools are frequently inspected, calibrated, and maintained to prevent avoidable issues.
- Source quality raw materials: Find reputable suppliers and conduct batch tests to ensure material consistency.
- Embrace proactive measures: Instead of only reacting to defects, focus on preventative actions that reduce the likelihood of defects in the first place.
- Document everything: Maintain comprehensive records of every production run, which can be invaluable for traceability and continuous improvement.
Many businesses choose to work with a partner that provides CNC machining, which includes quality control. You’ll benefit from a specialized provider rather than learning CNC machining and quality control from scratch.
GN Corporations is an industry leader in CNC machining, and we’ve built our reputation by providing reliable services and demonstrating commitment to quality for over 50 years. Would you rather have the experts handle your CNC machining?
Reach out to us today to learn more about how we can help.