Quality 4.0: Quality Management in the Digital Era
Industry 4.0, Manufacturing 4.0, the digital transformation. Call it what you will, but the fourth Industrial Revolution is upon us, and it’s on the tip of everyone’s tongue these days.
While all of us know about the Industrial Revolution from history class and how it streamlined manufacturing practices significantly, few know about the significant changes the manufacturing industry has experienced over the years.
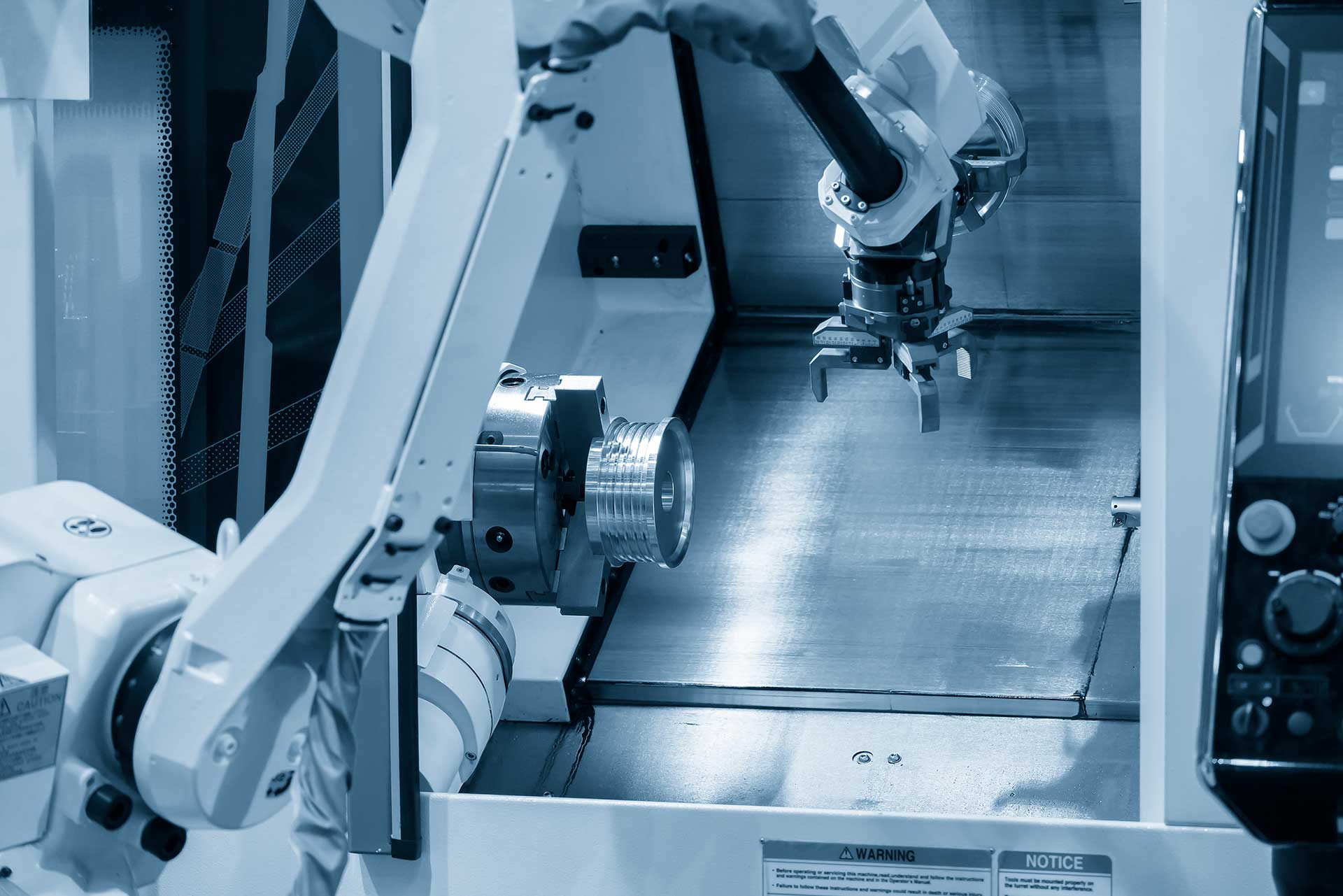
These analogous changes to traditional quality approaches like quality control and assurance have greatly transformed the industry.
So, what do these changes look like in practice?
Quality 4.0 is where we are today, and modern manufacturing facilities can’t afford to ignore these changes.
What Is Quality 4.0?
Any Industrial Revolution involves a paradigm shift in the way we approach workplaces, markets, and manufacturing, catalyzed by exponential improvements in disruptive technologies.
An analogous change in quality standards also occurs and dictates how we apply these new tools and technologies to increase production efficiency.
Quality 4.0 leverages the use of artificial intelligence, machine learning, and human supervision to improve processes and quality management practices resulting in operational excellence and better quality products and services.
GN Corporations Inc. has implemented quality 4.0 as part of its commitment to embracing Industry 4.0. We leverage new machine learning methods to analyze and utilize data collected by sensors throughout the factory floor to unlock new possibilities for reducing defect rates and continuous quality improvements for our partners.
The Evolution of Quality Management In Manufacturing
When covering Industry 4.0’s meaning, it’s worth knowing the context of how the previous Industrial Revolutions led to its development.
Industry 1.0 (Prior to the 20th Century)
Industrial infrastructure began around the late 19th century with the rising use of water and steam power in the production process, which could output products at higher efficiency and consistency compared to traditional independent craftsmen and artisans. Similar advancements in shipping and transportation were also possible now to ship those finished products to users.
Quality at this point was mostly measured through inspection, and quality teams focused almost entirely on yield. Little attention was given to other aspects like waste elimination and working conditions.
Industry 2.0 (Early 20th Century)
Steam power eventually gave way to electricity, which began to power the motors used in more automated production lineups. This resulted in much better performance across the industry.
However, Quality 2.0 still focused largely on yield, and factories mainly focused on getting the minimum acceptable level of quality out the door in order to boost profitability.
Industry 3.0 - The rise of quality management systems (Late 20th Century)
With the technological developments in the late 20th century, robotic systems began to take hold. Fewer human employees needed to be on the factory floor at this point, and new changes resulted in more efficient production procedures, the evolution of quality processes, and the development of new standards. The International Organization for Standardization (ISO) started up around this time.
Quality 3.0 was where quality finally took center stage. New focuses included customer satisfaction and continual improvements to the production line. Quality leaders in manufacturing companies began to focus more on the cost of quality and the importance of investing in quality management systems to detect product quality issues and reduce future costs of dealing with product failures.
Industry 4.0 (21st Century and Beyond)
Today, we’re seeing the introduction of even more automated processes empowered by digital interfaces, the Internet, and emerging technologies like machine learning and artificial intelligence.
Quality 4.0 was naturally digital quality management. Digital processes could not only make adjustments quickly and easily but also adapt themselves to new working environments independently.
Humans continue to play a major role in decision-making. Quality managers became process designers rather than factory floor operators, and most staff are involved in systems design along with other roles.
How Do We Implement Quality Excellence at GN Corporations Inc.?
Quality 4.0 tackles three main areas when it comes to solving product quality challenges in manufacturing and digitally transforming production workflows.
- People: Quality assurance staff have new tools to perform root cause analysis and navigate their initiatives to success. They will take planning roles as opposed to the on-site enforcement of QA policies.
- Processes: The strategic planning phase will integrate quality considerations, including assessments of quality flaws in the supply chain.
- Technologies: Exponential growth in technologies will empower quality professionals to accomplish more in their organizations as long as they know how to use them.
We achieve these principles through the latest tools available to us. Machine learning algorithms and AI have found their places in forecasting roles, chatbots, and robotics, among others. But blockchain technology, which has gained major popularity in recent years, can be used to ensure transparency and simplify audits. Other companies are searching for new use cases for virtual reality, cloud computing, and the Internet of Things trend too.
The Main Components of Quality 4.0
GN Corporation also defines the following essential components for any Quality 4.0 initiative:
- Data: Quality 4.0 is largely data-driven, and a lack of quality data and metrics is usually cited as a major reason why some programs fail.
- Analytics: Good decision-making hinges on strong analytics, so it's important that staff members have access to advanced analytics tools and digital dashboards to analyze and share information.
- Collaboration: Digital tools that have replaced manual processes are able to bridge gaps and knock down silos between separate business workflows. This way, data can be synchronized, and QA processes can be unified.
- Scalability: Large enterprises working with a growing number of devices and data need to leverage cloud computing and other Quality 4.0 tools to boost scalability.
- Quality Management Systems: Connectivity is one of the main selling points of Quality 4.0, and a quality management system is able to integrate all quality-focused processes together throughout a product’s production cycle to eliminate errors and delays.
- Compliance: Automation helps cover compliance responsibilities more comprehensively.
- Leadership: Support from upper management is absolutely vital. Quality managers must convince upper-level executives of Quality 4.0’s importance by tying their objectives with the overall goals of the business.
On top of these principles, find a way to establish a culture of quality within your organization. Company culture is a key factor to successfully implementing Quality 4.0.
Position for Future Success by Partnering With an Industry 4.0 Leader in Manufacturing
At GN Corporations Inc., we embrace the future of quality and have adopted Quality 4.0 as part of our company culture and organizational excellence.
Not only have we invested in predictive analytics tools to continuously improve our quality management processes, but we've also committed to advancing the state of the art in the global manufacturing industry.
Partner with us to learn
more about Quality 4.0, so you can integrate its principles and tools into your workflows.